Our Remote Operations Center Saves You Money — But Not Just In The Way You Think
Harnessing the Power of Remote Operations Centers for Efficiency and Savings
Remote operations in all industries have become more common in the last few years — from healthcare to education, and of course to oil and gas. A decade ago, managing a drilling operation from hundreds of miles away would seem impossible. However, with the right technology, processes, and people, it’s more than possible — it’s the direction the industry is moving in today.
While some clients hesitate to embrace remote operations simply because they are unfamiliar with them, those who understand the cost savings and additional value a remote operations center (ROC) brings to the project never look back to doing things the conventional way. Within just a few weeks, they realize how valuable a remote operations center is and how much money it can save them in the long run.
ProDirectional is a leader in remote operations, having completed over 30,000 remote tours with a group of highly trained remote operations specialists. And while we certainly save our clients thousands of dollars on each project, it’s in a different way than you might expect.
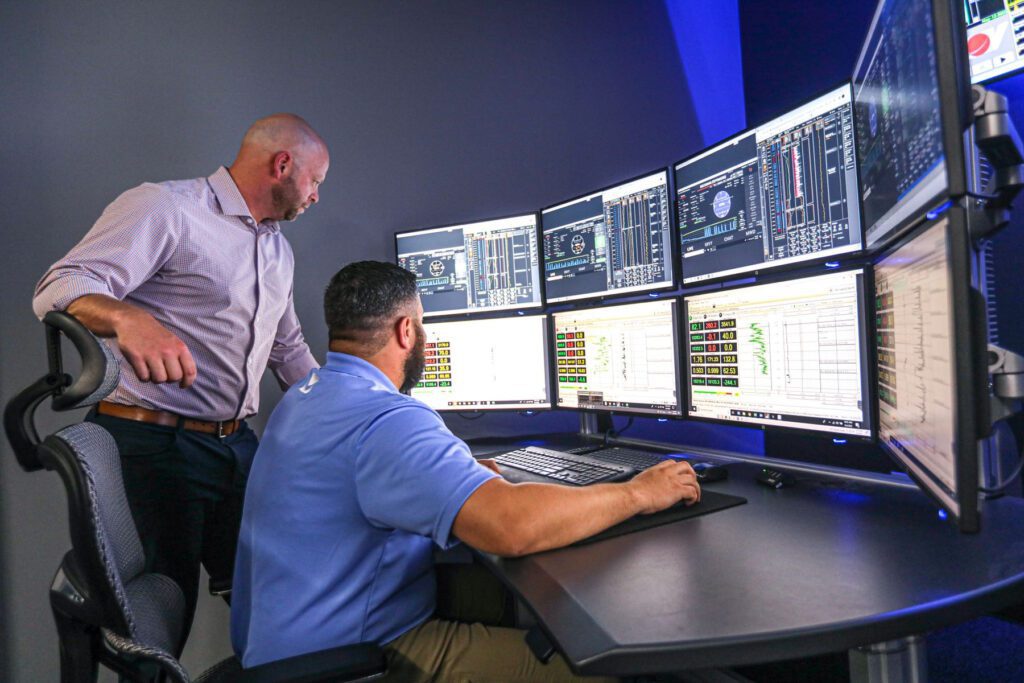
Going beyond predictable cost savings
You may expect that the main way to reduce costs for the client with a remote operations center is by minimizing the number of personnel on site. As a result, you have a lower day rate and a lower cost of service delivery. All of this is true — by having a remote operations center we are able to reduce the day rate and cost of service delivery for our clients. However, this is only the tip of the iceberg when it comes to cost savings.
At ProDirectional, we’re never satisfied with the status quo, and are always looking for ways to go above and beyond for our clients. We know that the only way we can succeed is when our clients succeed. This is why the main way we offer cost savings for our clients through a remote operations center is with value creation.
Adding value through expertise
Our remote operations center is manned by our team of remote operations specialists, all of whom have considerable experience working on rigs. We have a central location for our remote operations at our headquarters, where we also have our directional and MWD coordinators, technical services team, and engineers, all of whom act as resources for our remote operations team.
Instead of having just one person at the rig, our clients have this exceptional team of professionals available to troubleshoot any type of problem that occurs. We can escalate the issue quickly to the required experts, gather the information we need to solve the problem, and implement the solution within minutes. This simply isn’t possible without a remote operations center in place.
Having so many eyes available to look at the issue provides a wealth of expertise and experience. We even had a situation where the pressure signature being generated by the rig pumps resulted in all the standard filtering protocols being ineffective for decoding. In this situation, our remote operations team engaged with the right resources to get a custom filter written into code and deployed it quickly in real time in order to decode the data at the surface and communicate with the tools downhole. If our client didn’t have remote operations expertise available to them, this problem would have taken days to solve, resulting in non-productive time (NPT).
What is all of this expertise worth to our clients? While it’s hard to put a dollar amount on it, most would agree it’s in the tens of thousands of dollars at least — especially when you consider the amount of NPT we’re able to help our clients eliminate.
Ensuring we support you 24/7/365
At ProDirectional, we understand that our clients’ drilling operations run 24/7/365. That’s why our remote operations center runs 24/7/365 as well — and we don’t stop for anything. It’s a mission critical service, which is why we have built in multiple layers of redundancies, both at the center and at the rig, to ensure our support continues no matter what situation we’re in.
Our ROC has a built-in power system redundancy, three levels of communication backups, a detailed disaster recovery plan, and extreme weather event protocols. In addition, we have redundancies at the rig as well, ensuring we never lose communication between the center and the wellsite.
Not only that, but all of our remote operations specialists also have a full setup at home, so if there is ever a situation where they are unable to come into the center, they can connect from home to provide client support. Our communication platform is proprietary technology we have built for this purpose, and it can be used from anywhere to connect to the rig.
As a result of these redundancies, we have an impeccable record for delivering our remote operations service. There is no situation in which we cannot connect to the rig. The cost of total peace of mind? We think most would agree it’s priceless.
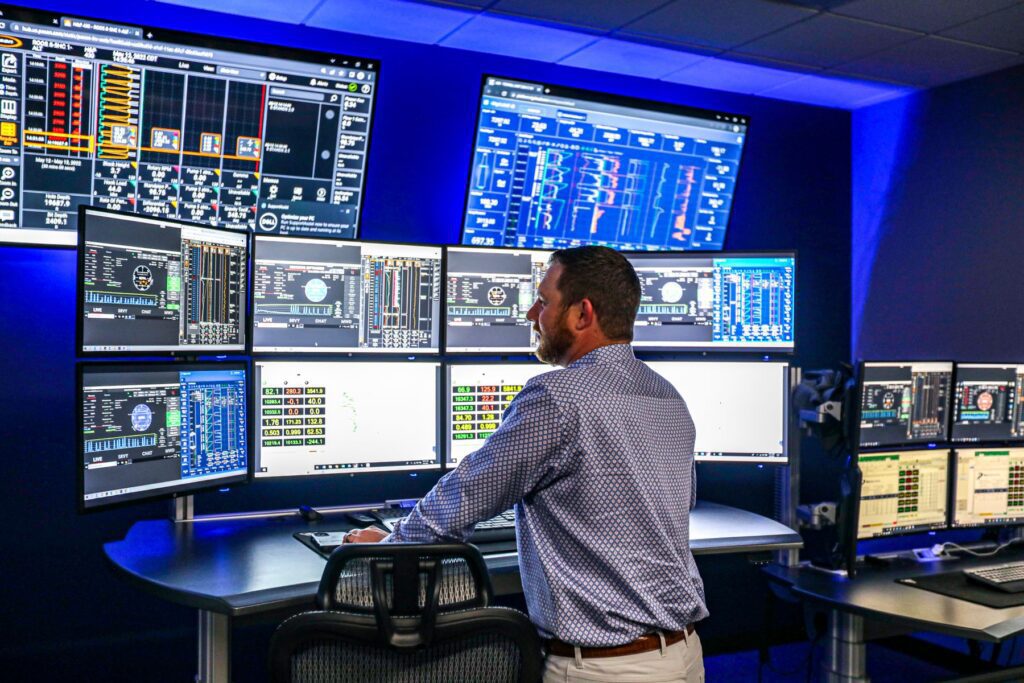
Our Remote Operations Center is at your service
While we have a robust remote operations center, we also have personnel in the field to support changing out downhole and surface equipment when necessary. However, when it comes to major troubleshooting, our remote operations center can handle anything that comes their way — operating in this way is second nature to us after tens of thousands of tours.
Our remote operations center can completely change the trajectory of your project, eliminate NPT, and ensure any issues are resolved immediately. Get in touch with us today to discuss how the remote operations center can benefit your project.
Recent Articles
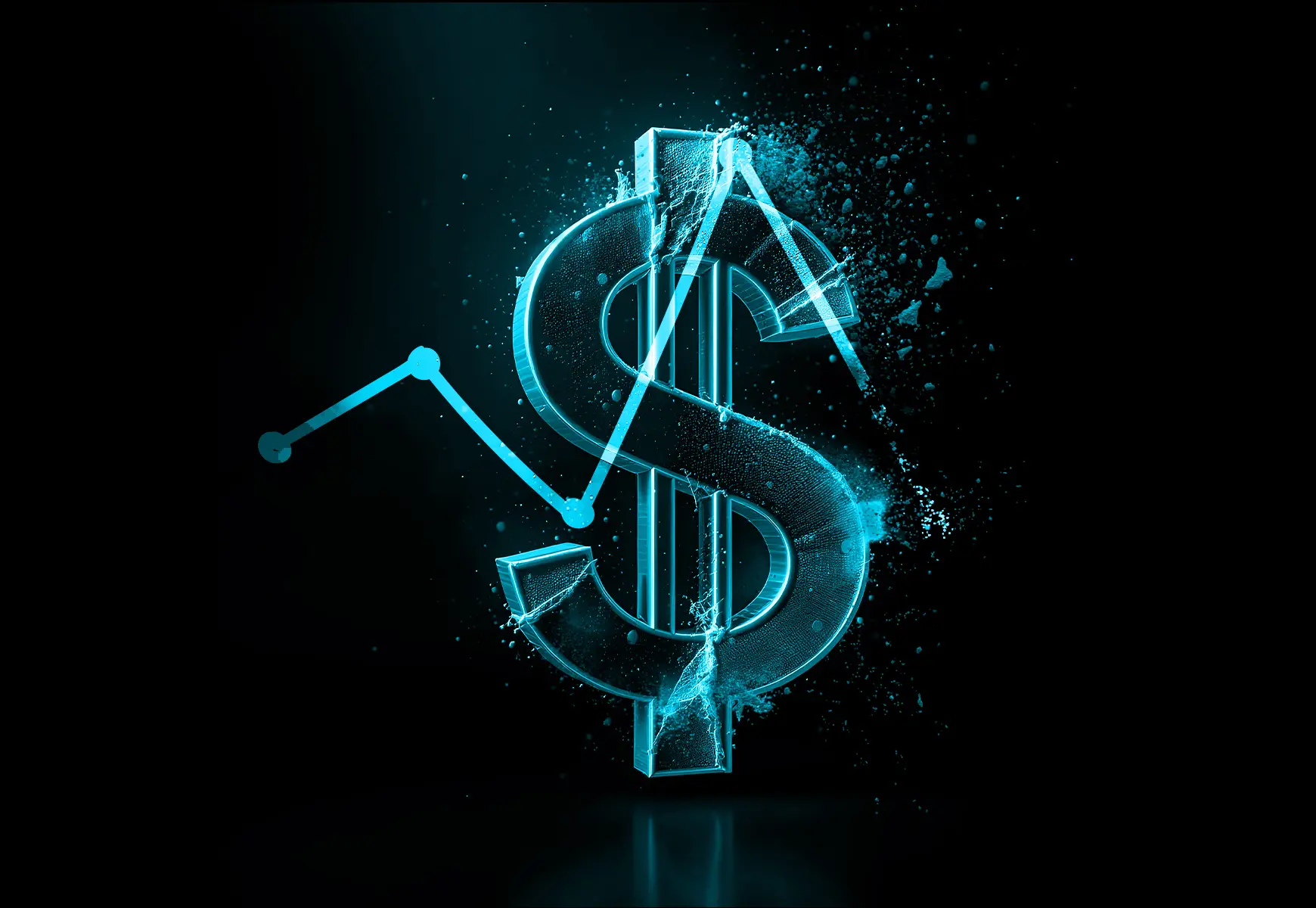
Why Best Value Beats Lowest Price in Directional Drilling
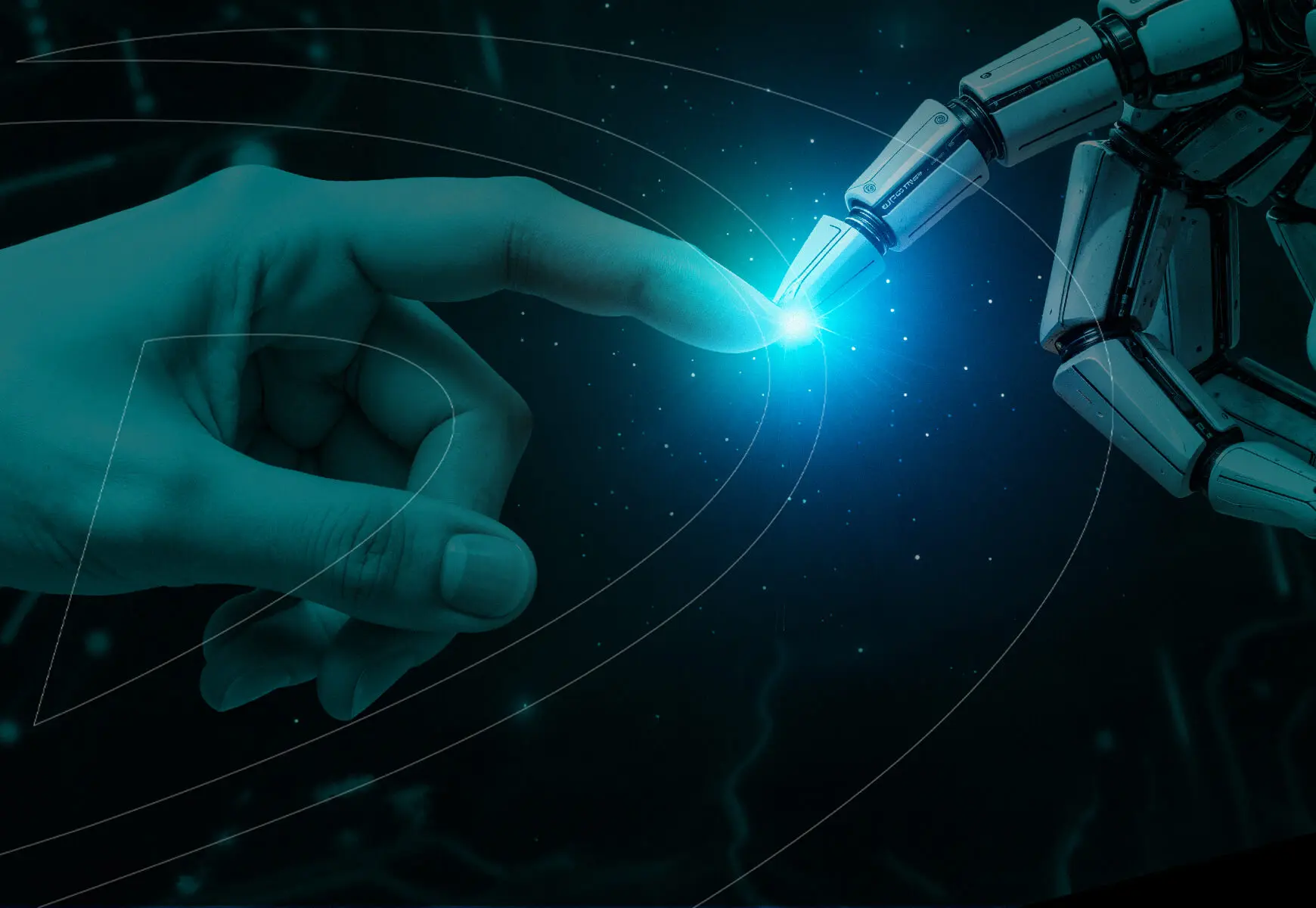
Automation in Directional Drilling: Why People Still Matter and How GUIDE ROC Delivers Both
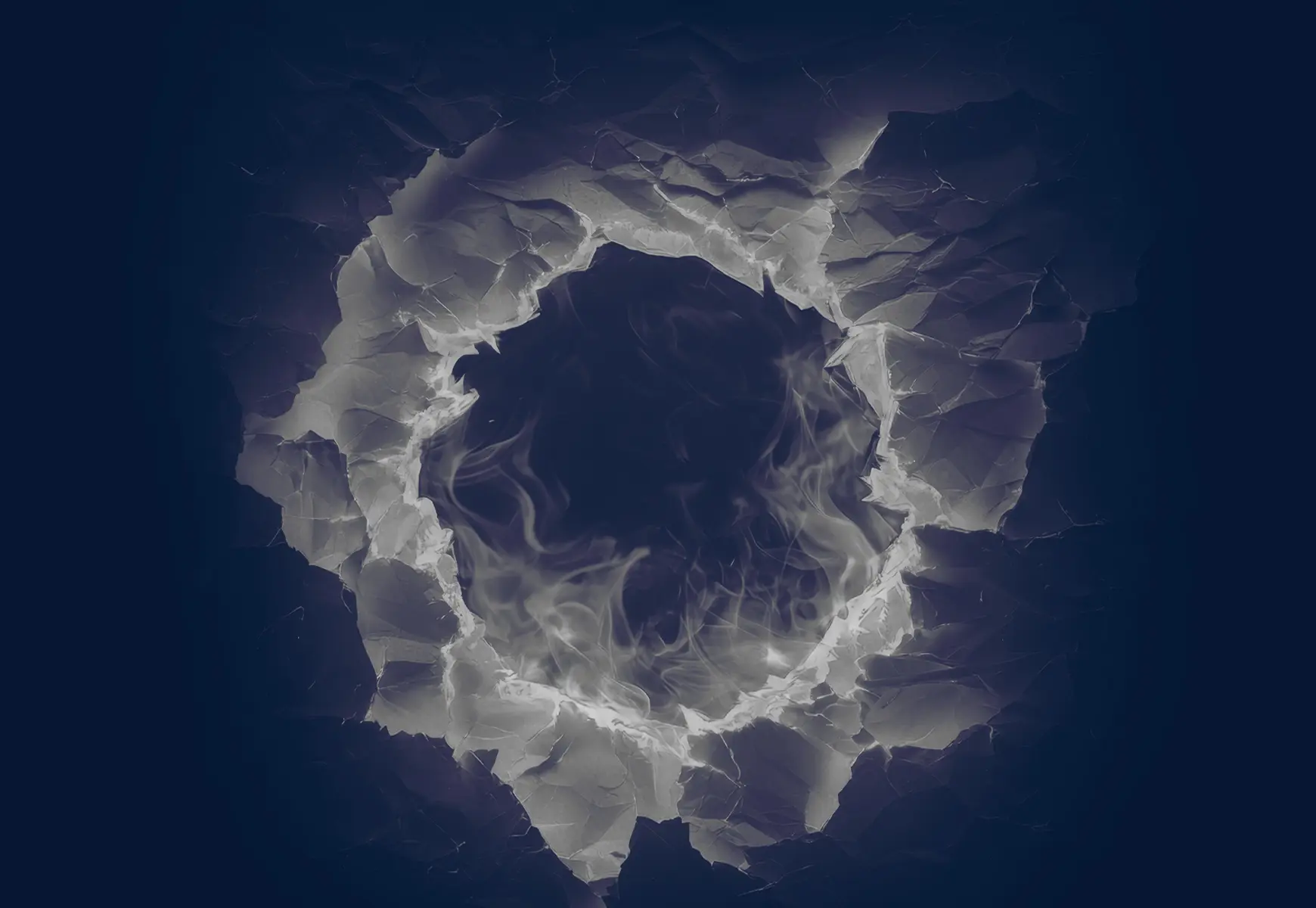
Turning Up The Heat: Providing Reliability in Hot Hole Environments
Built, Not Bought: The ProDirectional Advantage in MWD Services and Technology
A leap forward in rotary steerable system connectivity
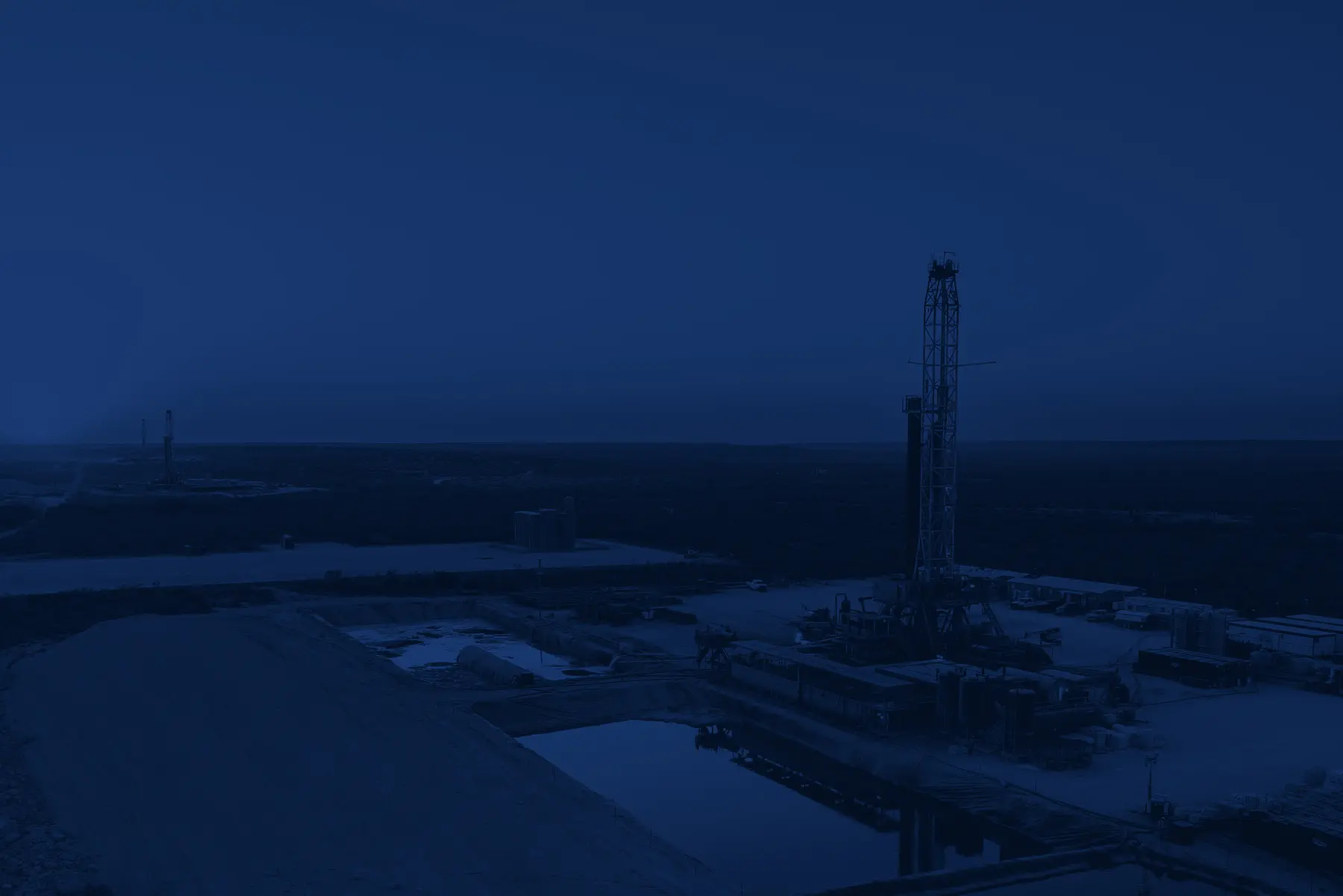
What client success looks like at ProDirectional
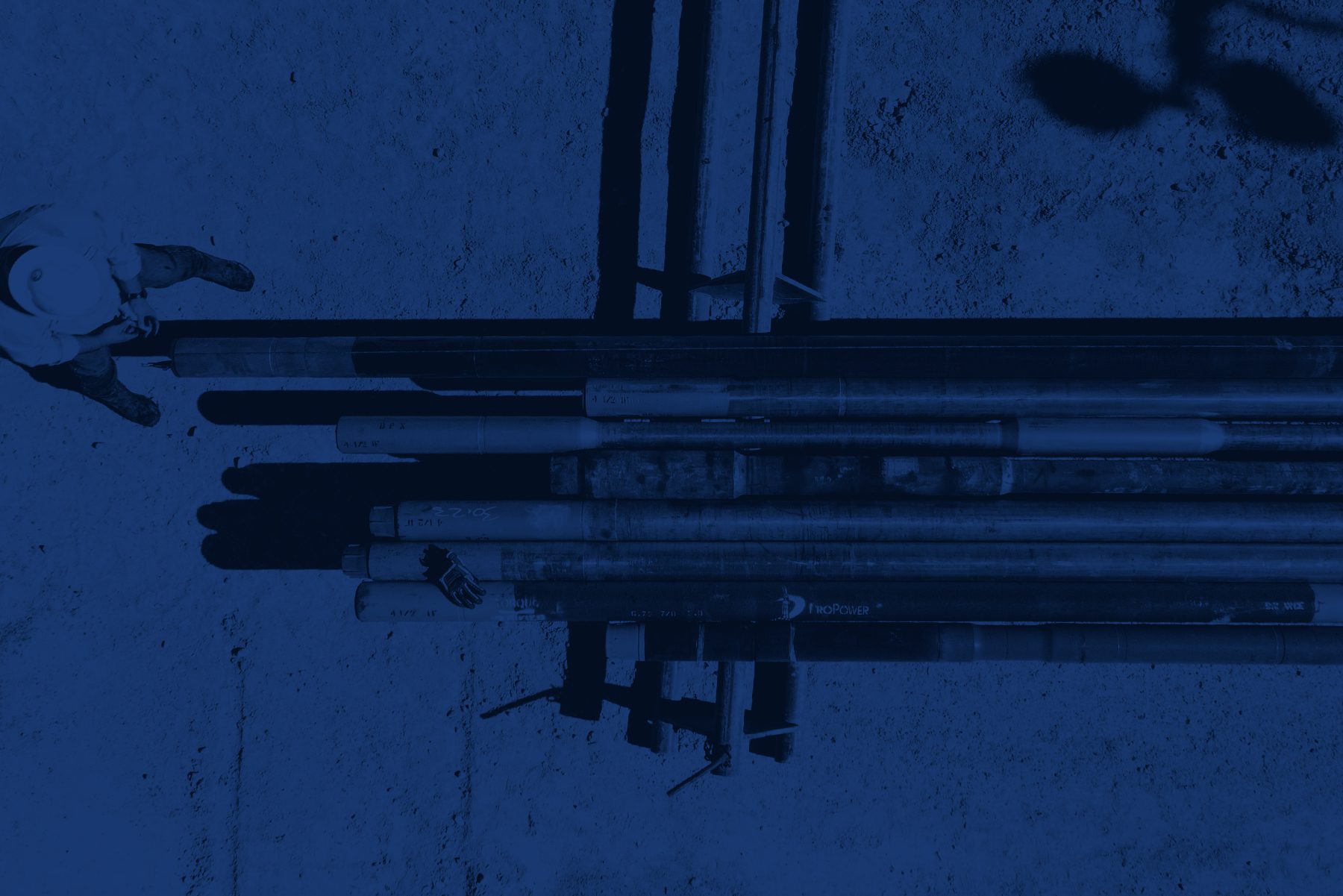
How does a mud motor work?
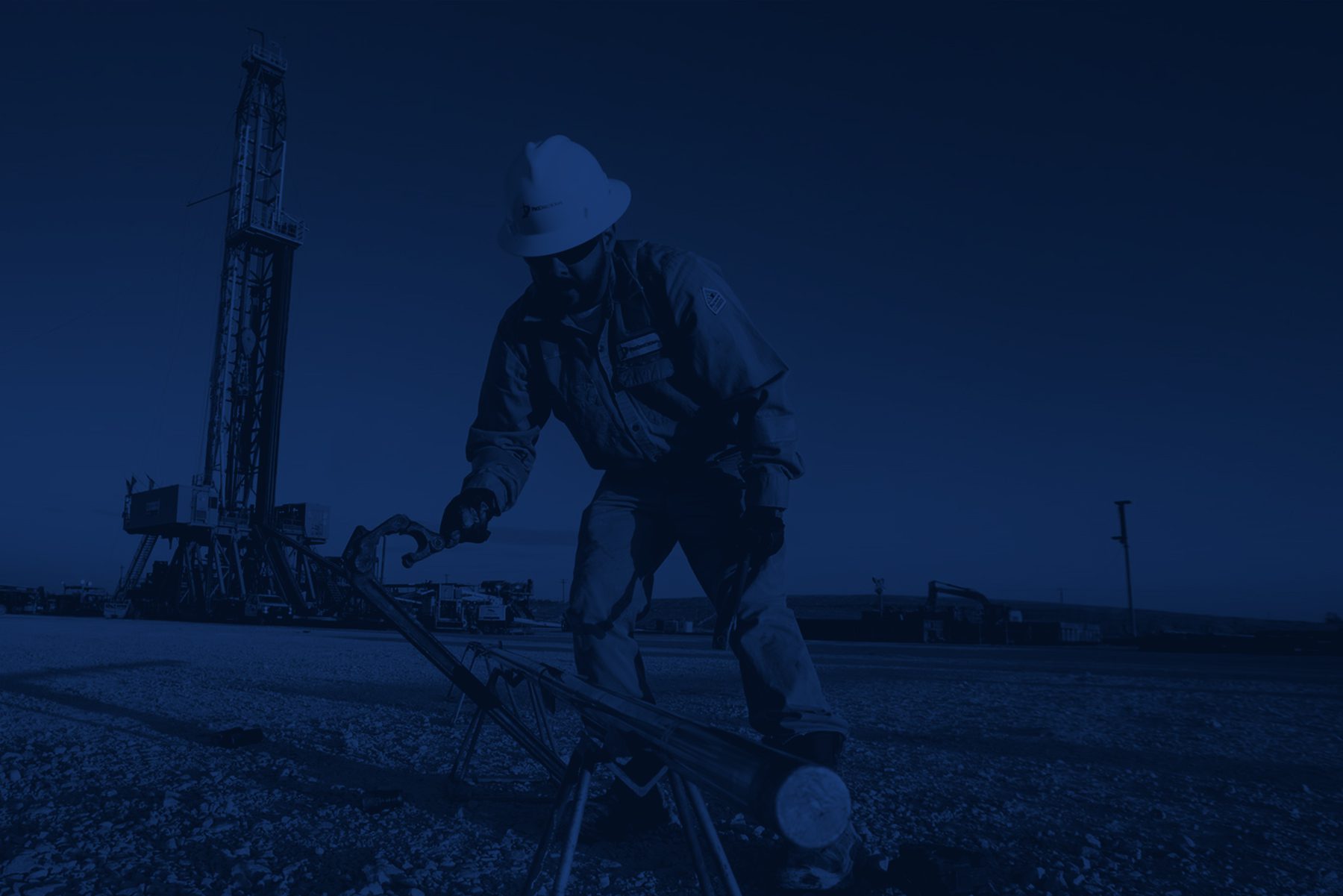
Application specific MWD tools and directional drilling technology will save you time and money
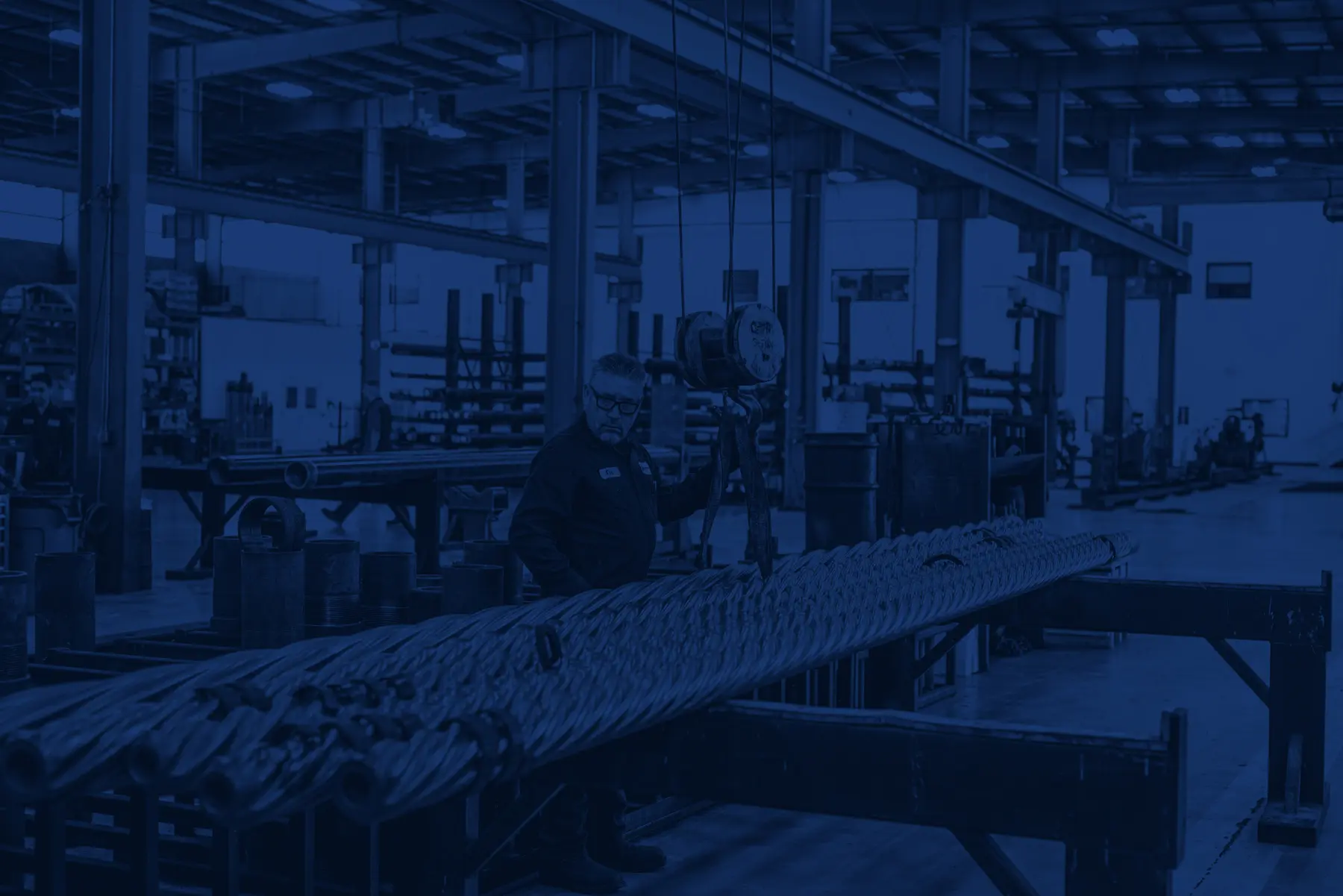
You can’t afford not to use highly engineered mud motor technology
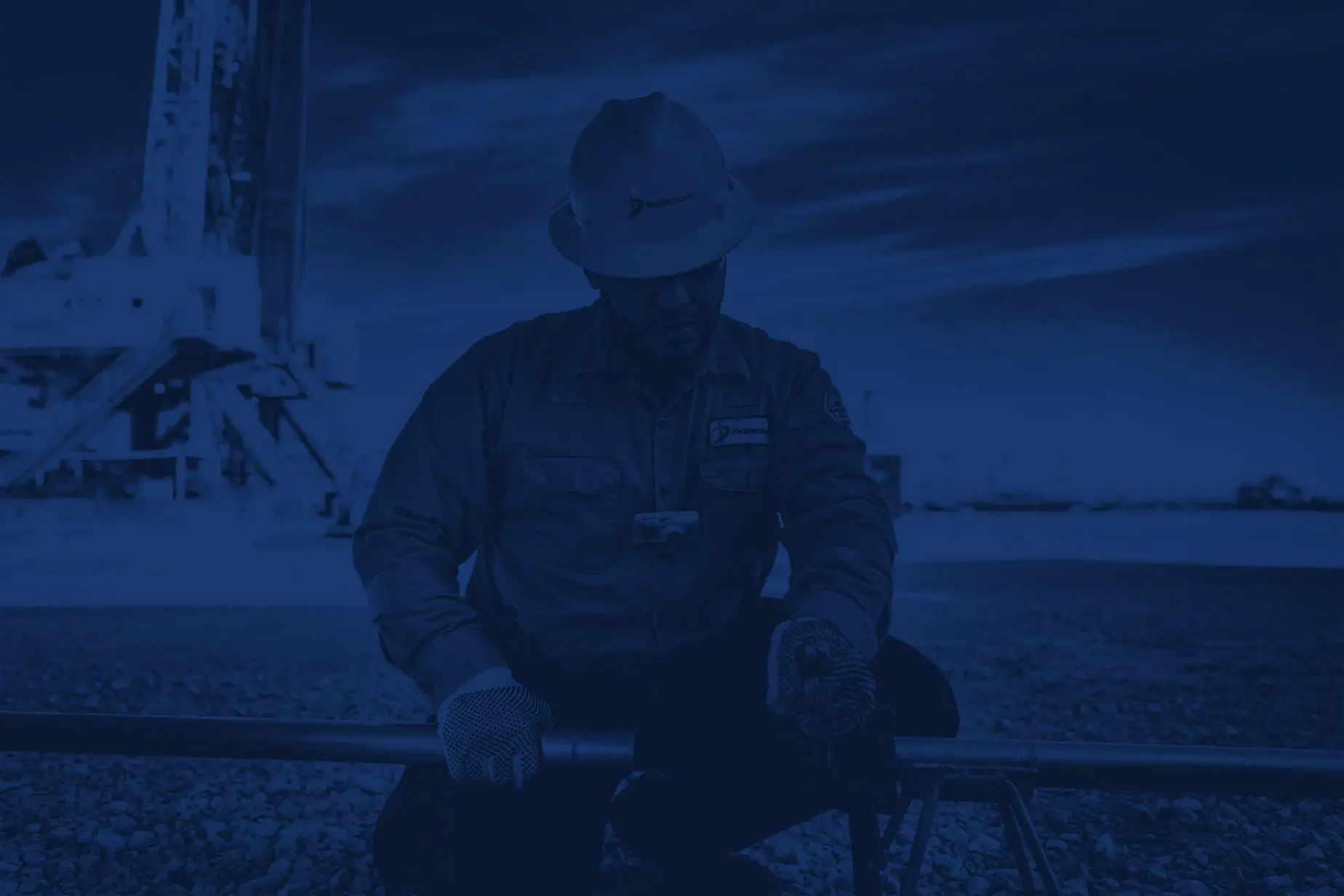