Turning Up The Heat: Providing Reliability in Hot Hole Environments
“Problem-solving leaders have one thing in common: a faith that there’s always a better way.”
Gerald M. Weinberg
The Challenge of High-Temperature Drilling
ProDirectional relentlessly pursues innovation and technology advancements to provide drilling services that are in a class of their own. The pursuit of energy has led to many technological advances, but it has also led to many technological challenges. One of those challenges is directional drilling in high-temperature environments. Hot hole wells are an increasingly puzzling challenge to energy providers as the oil and gas industry seeks deeper zones of pay, new plays, or expands into new energy sources such as geothermal energy.
As downhole temperatures increase, equipment capability is stretched to its limits. So, how does a drilling engineer mitigate the risks of drilling in high-temp environments?
Industry Demands and Regional Challenges
Existing plays in Texas such as the Eagle Ford Shale and Austin Chalk are current areas of exploration that have seen an increase in the demand for high-temp drilling experience. Other plays, like the Haynesville and Bakken have seen an increased need for successful hot-hole MWD tools. As temperatures climb in downhole environments, previously designed and used MWD tools are seeing failures that drive up costs for drilling projects. Time lost for repairs means time not drilling. Time lost drilling means time not producing. This is critical to major and smaller producers, both.
Advanced Testing and Preparation
How do we reduce the NPT that customers are exposed to? Our focus lies in deploying the strongest possible defense through rigorous testing and design processes that exceed industry standards. This commitment extends beyond our design phase to the pre-deployment stage of our tools. Before our equipment hits the road, we verify its ability to perform at the highest level. We defend against the unknowable in the best way possible by over-preparing.
The Power of Redundancy
While our equipment undergoes thorough preparation before leaving our facilities, we recognize that not every possible failure can be prevented. MWD tools face extreme and tortuous exposure while doing their job, with heat limits that can overcome current hardware and impact shock that can break even the sturdiest internal components. This reality drives our redundancy feature in gamma tool design, providing users with assurance that two is one and one is none.
The key to success in horizontal drilling lies in accurately knowing the bit’s location within the zone of interest. When this capability fails, drilling time is typically lost due to pulling out of the well to replace the gamma tool. Our tools, however, feature the ability to swap out the gamma tool live while in the well at depth through our redundancy approach. This capability saves critical hours of NPT, reinforcing our customers’ trust in keeping them on schedule, on budget, and on task.
Quality Through In-House Excellence
One of the biggest factors in our success working in plays that see temperatures up to 200° C is our in house maintenance and design. Standing behind our tools comes naturally because we oversee every aspect of their preparation for the field.
Building Long-Term Success
ProDirectional builds trust and strong relationships with customers because that drives mutual success. Twenty years under the ProDirectional banner, combined with countless years of individual experience amongst our team, demonstrates our proven ability to solve customer problems. Hot hole wells represent another arena where we answer our customers’ calls, creating better paths to profitable assets.
If you have directional drilling needs in hot-hole scenarios, give us a call to discuss how ProDirectional can help you reach your target.
Recent Articles
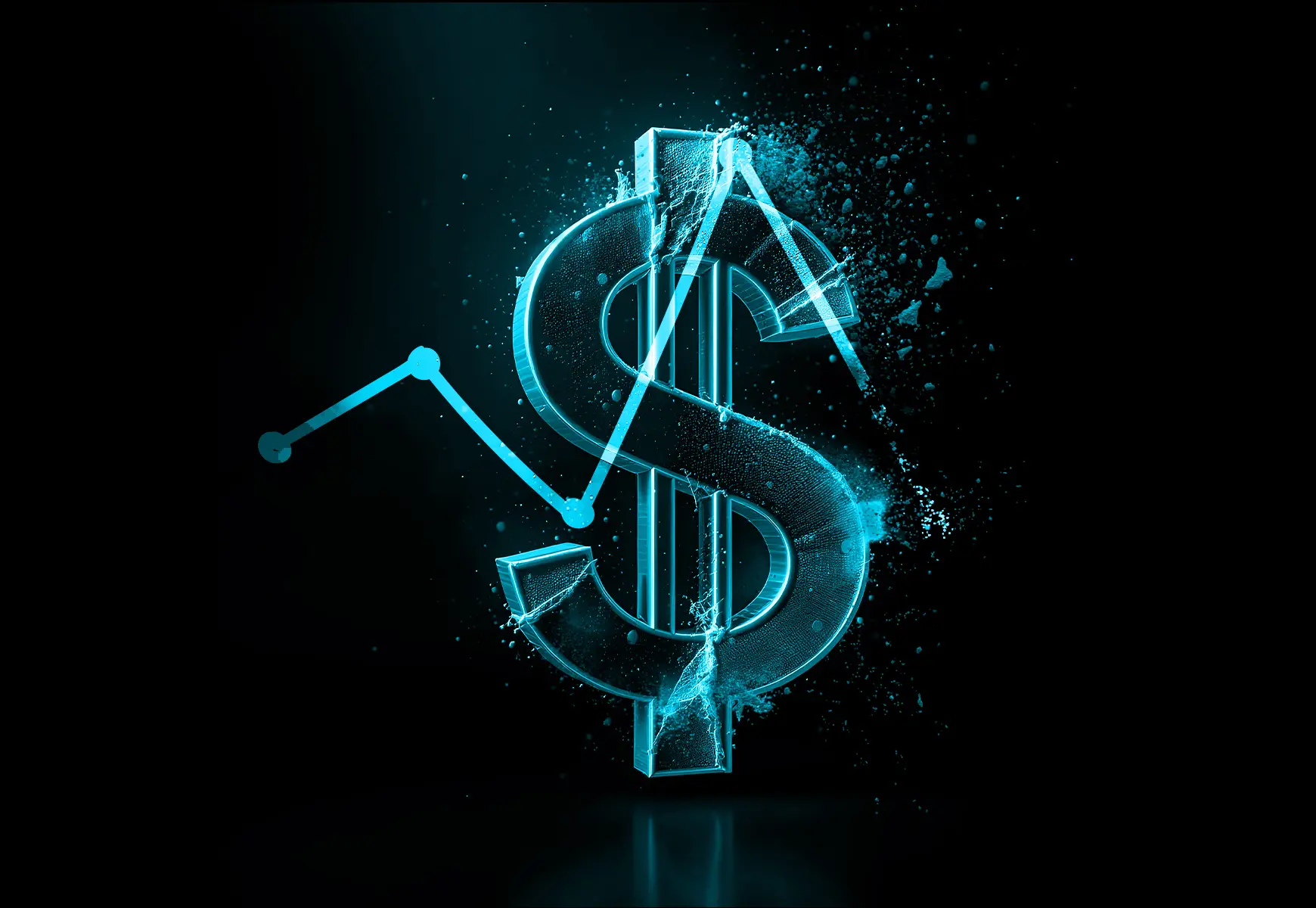
Why Best Value Beats Lowest Price in Directional Drilling
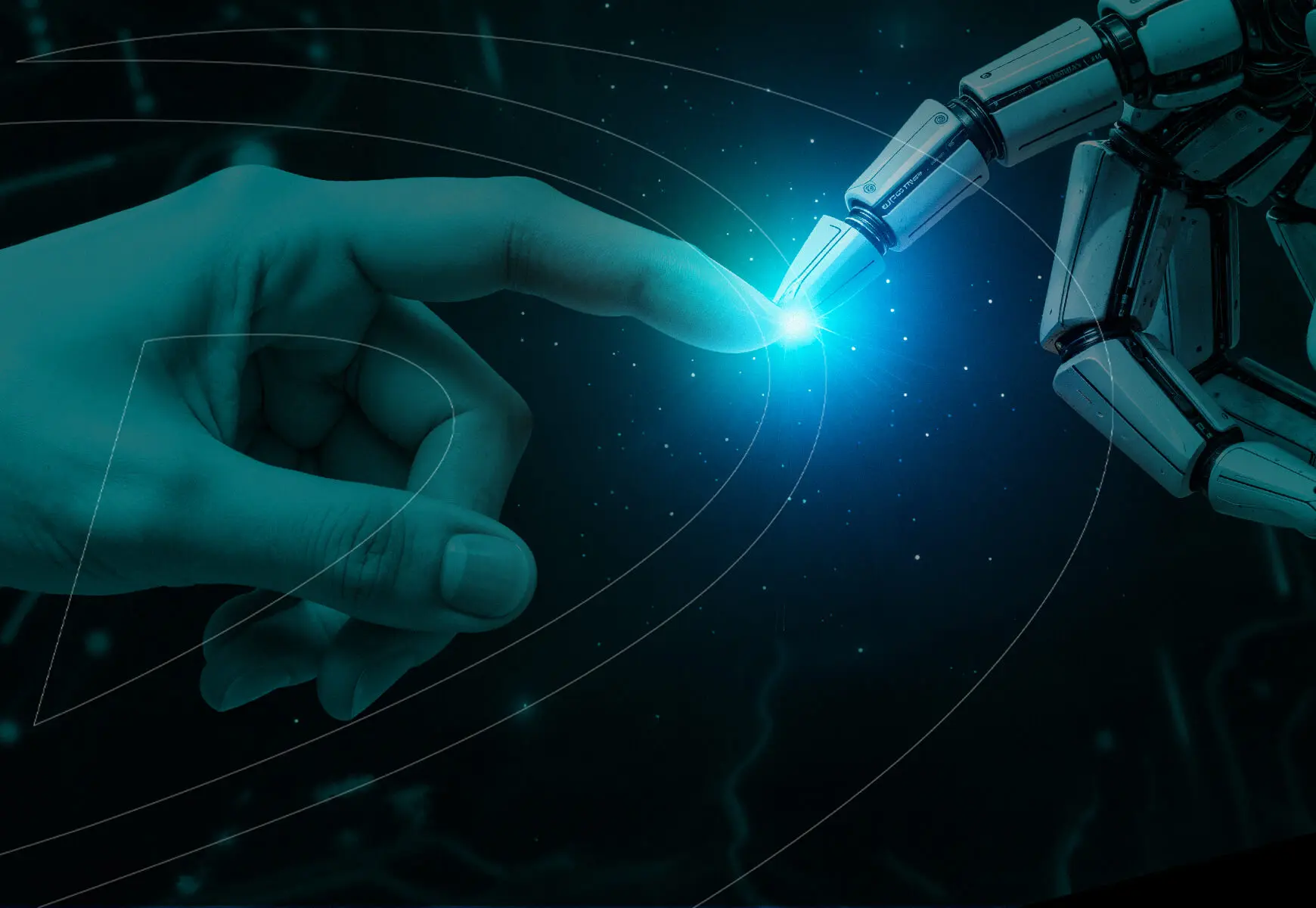
Automation in Directional Drilling: Why People Still Matter and How GUIDE ROC Delivers Both
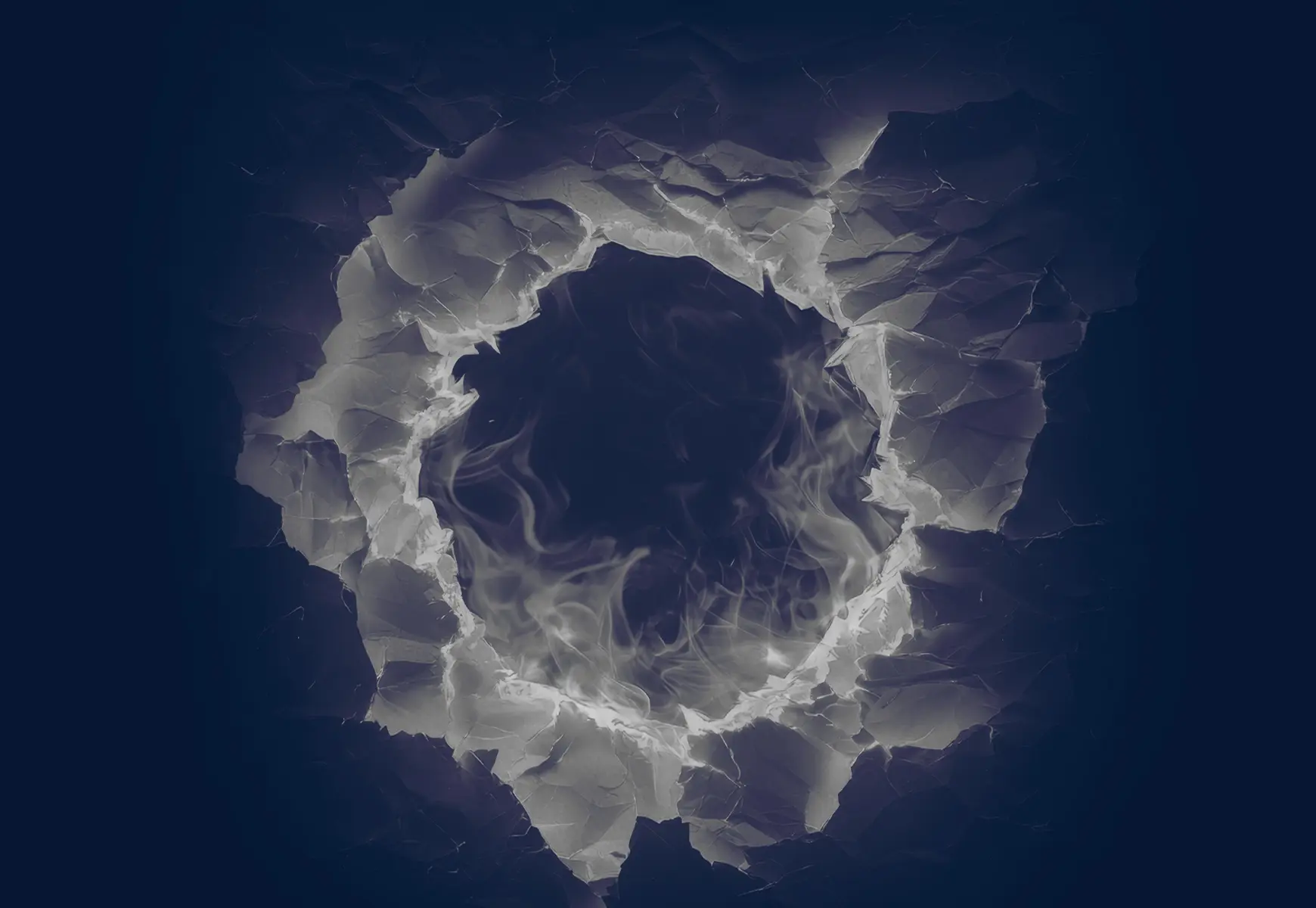
Turning Up The Heat: Providing Reliability in Hot Hole Environments
Built, Not Bought: The ProDirectional Advantage in MWD Services and Technology
A leap forward in rotary steerable system connectivity
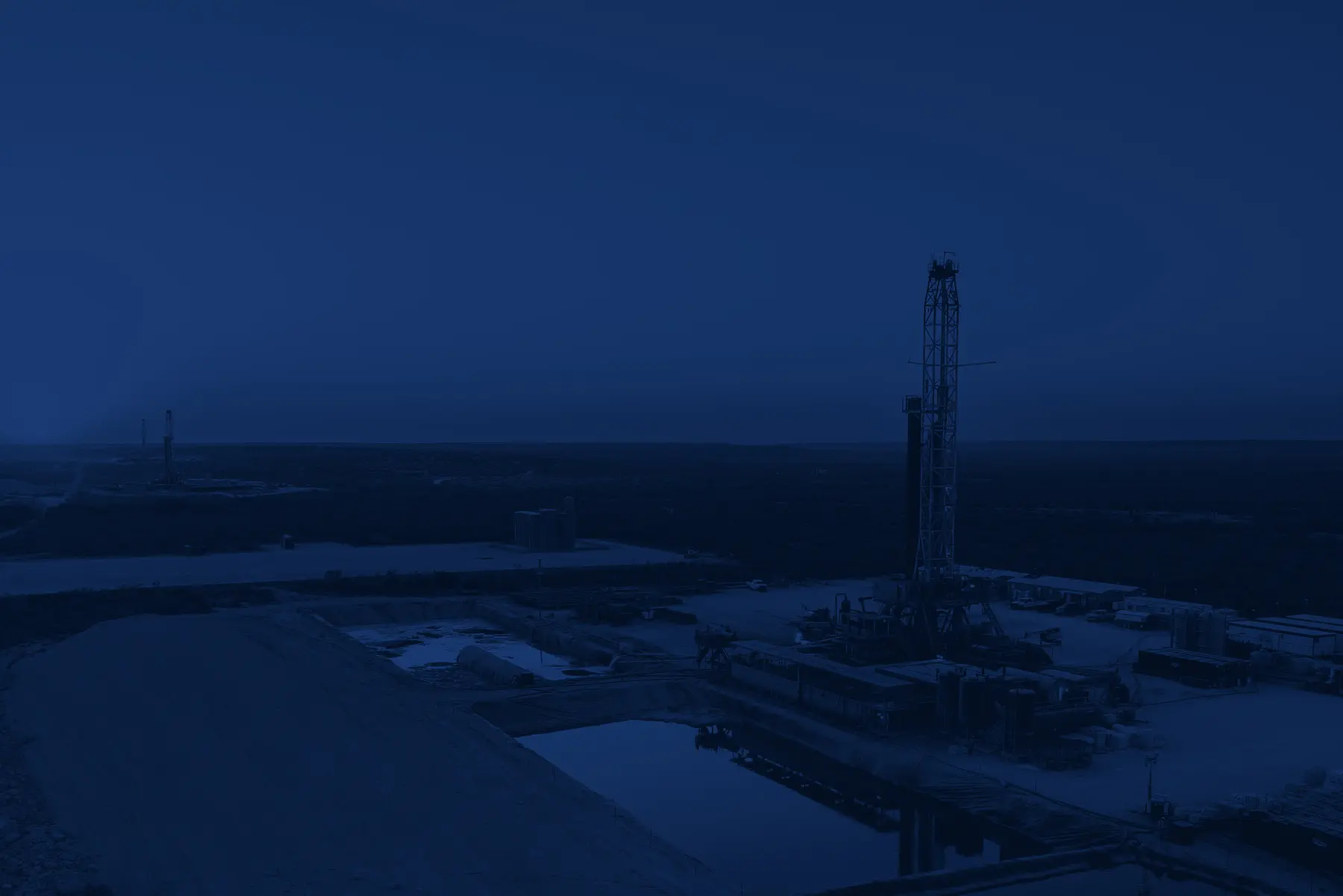
What client success looks like at ProDirectional
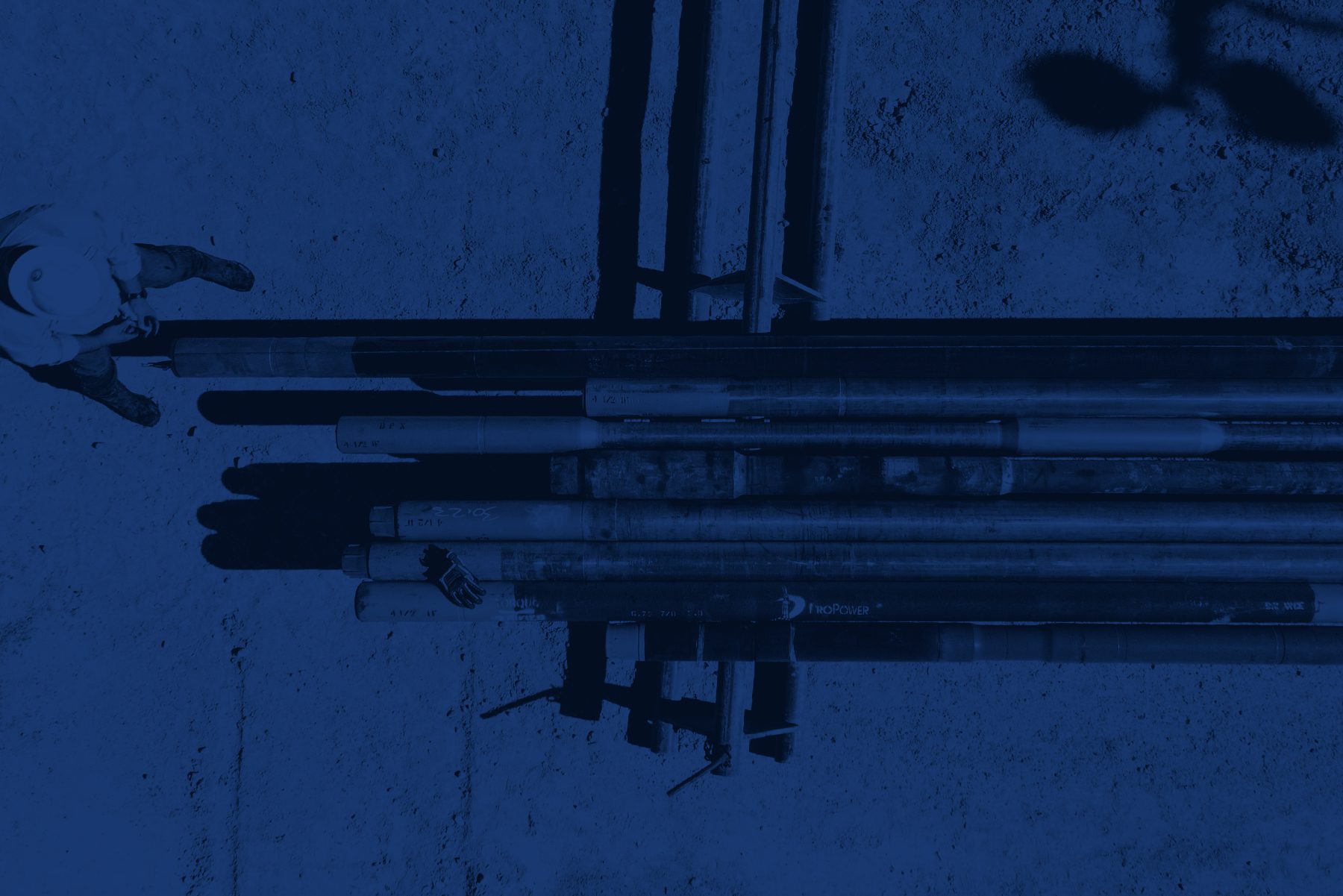
How does a mud motor work?
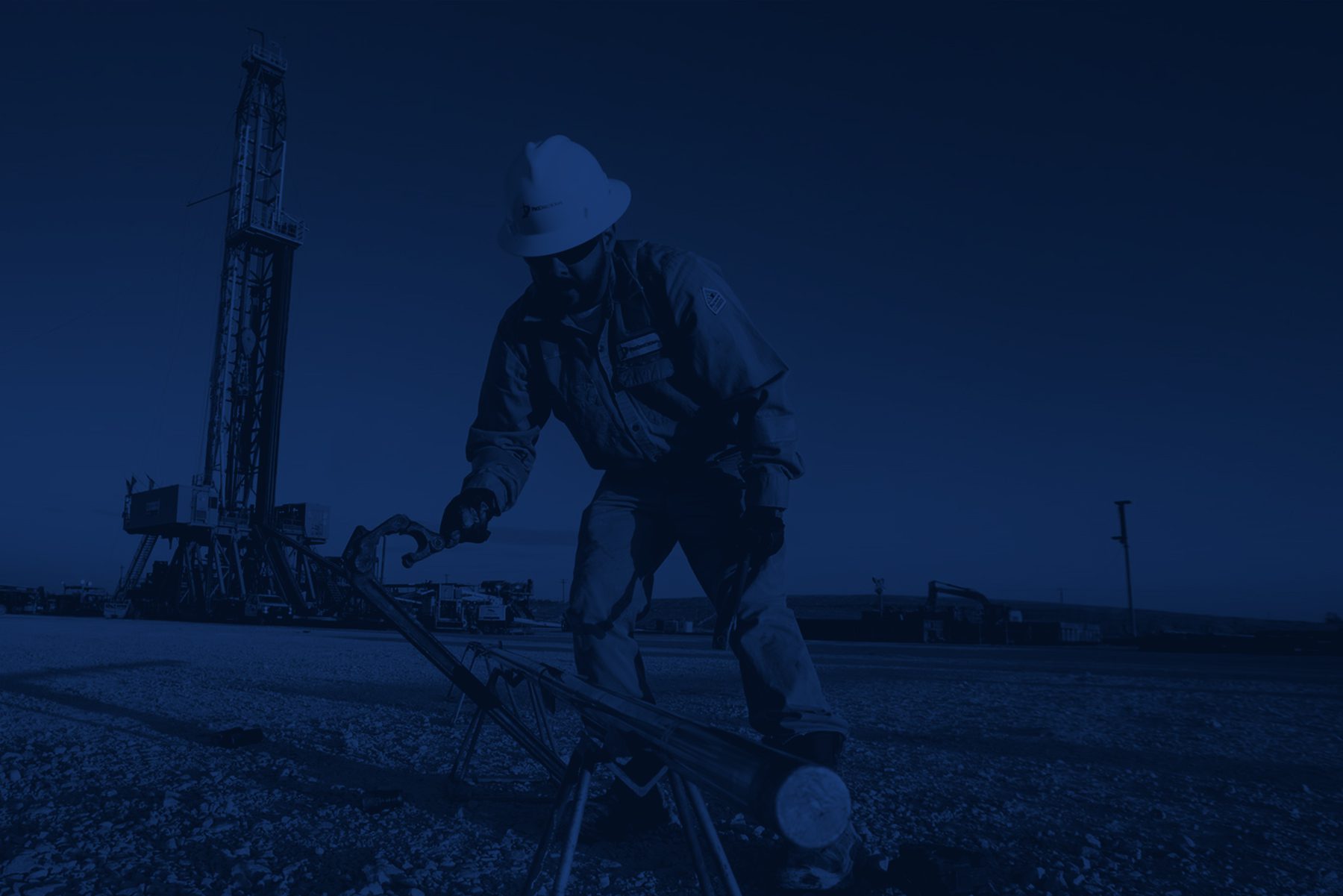
Application specific MWD tools and directional drilling technology will save you time and money
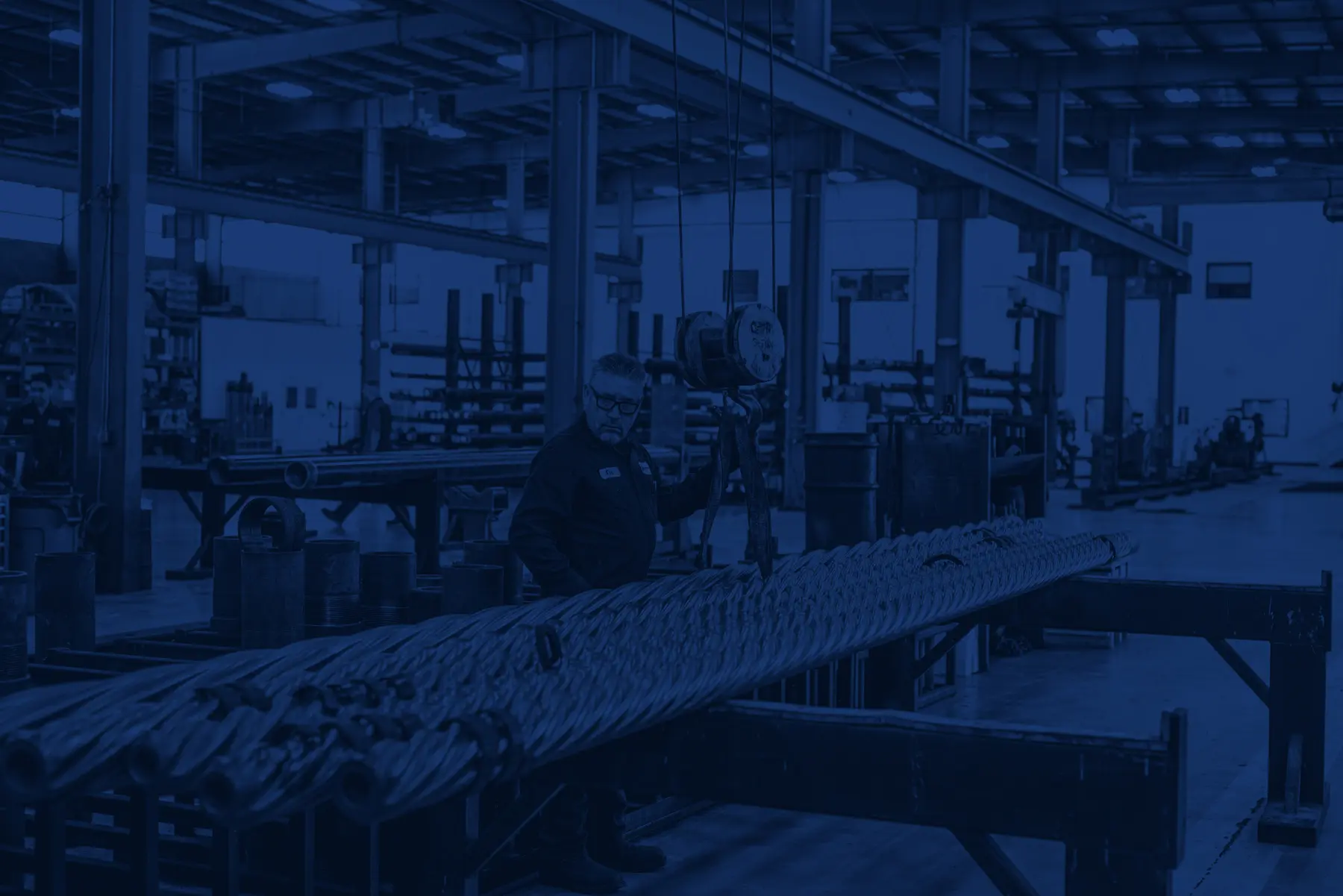
You can’t afford not to use highly engineered mud motor technology
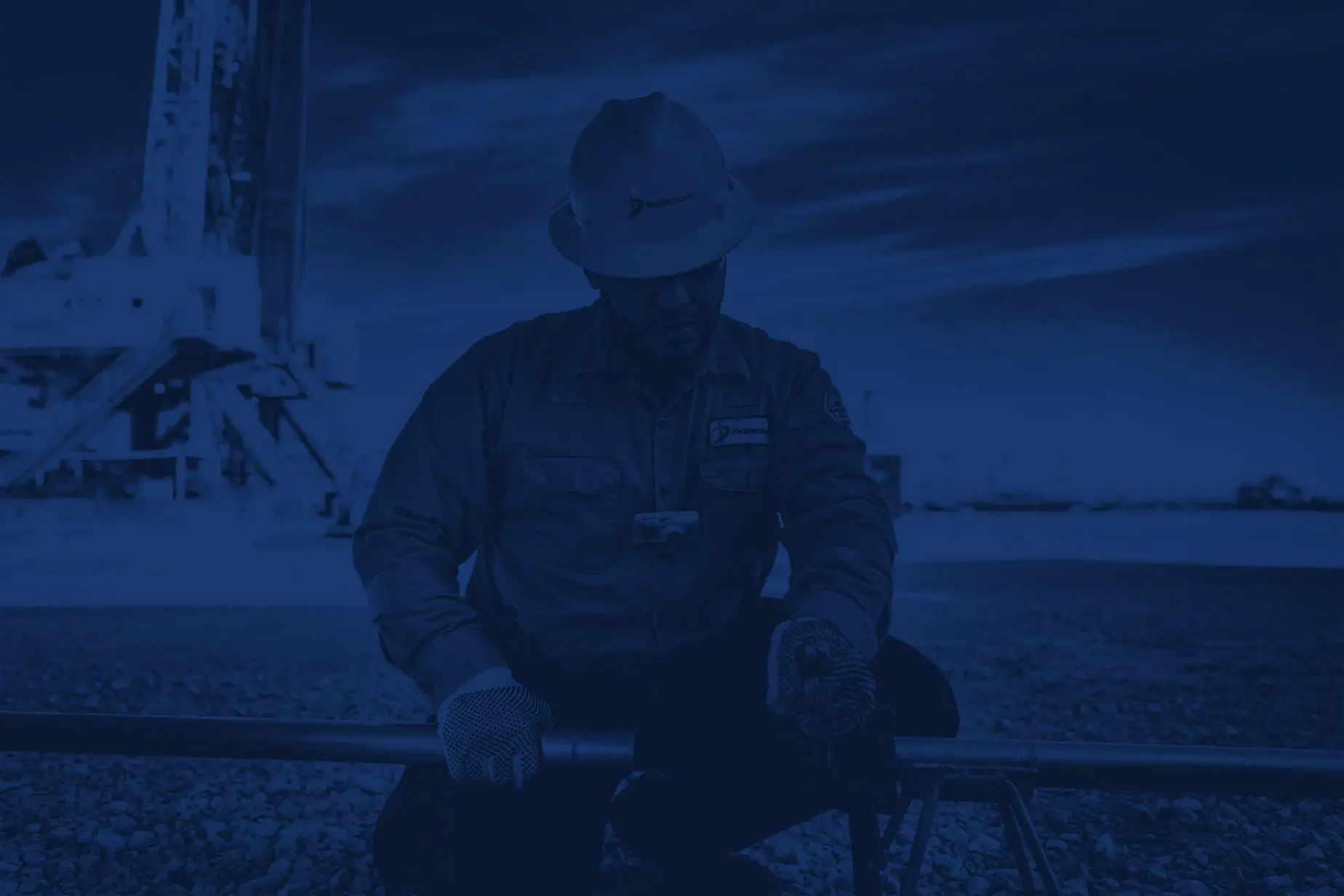