How does a mud motor work?
Enabling operators to drill wells without non-productive time is what we do everyday.
Our customers know us for our constant reliability, in everything from our equipment to our service.
So, what makes us so reliable in the first place? It has everything to do with our application engineering process.
Instead of taking an off-the-shelf approach and purchasing all of our motor components, we optimize the equipment to better meet the needs of each operator and the environment in which they are drilling. Mud motors are an incredible piece of equipment that is responsible for faster and more efficient drilling, and we take great pride in the motors that we produce.
Ever wondered how a mud motor actually works and the different components it contains? You’re about the find out.
The mud motor: breaking down each major component
A mud motor has four main sections: the lower-end bearing pack, the drilling motor transmission, the bent housing, and the power section. At ProDirectional, our mud motors are based on the industry’s most trusted power sections, which we combine with our highly engineered lower-end design in the bearing and transmission sections. Together, this creates the most reliable mud motor in the industry.
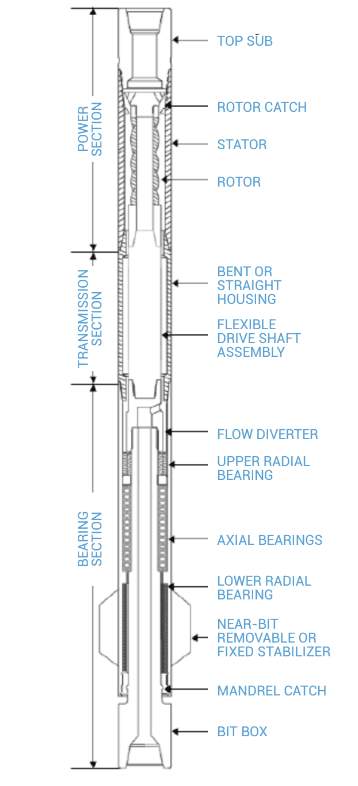
The lower end bearing pack
This section of the mud motor includes the flow diverter, upper radial bearing, axial bearings, lower radial bearing, near-bit removable or fixed stabilizer, mandrel, and bit box.
The lower end bearing pack transfers the torque and RPM, which is generated by the power section and the top drive of the rig, to the drill bit. It also connects the rest of the mud motor to the drill bit. The lower end bearing pack includes a number of bearing surfaces and shafts which are designed to transfer power by carrying the weight on bit and transmitting torque.
The drilling motor transmission
The job of the mud motor transmission is to connect the rotor to the lower end bearing pack. It also converts the motion of the rotor, which is eccentric, into a concentric rotary motion, which results in more consistent energy transfer to the drill bit. The drilling motor transmission essentially carries the torque and rotary motion that is created by the power section to the lower end.
At ProDirectional, we have motor sizes for every interval from surface to slimhole drilling applications.
The bent housing
Sometimes, the bent housing section is considered to be a part of the mud motor transmission section. However, because it plays such an important role in directional drilling, we are detailing it as a separate component.
In directional drilling, the bent housing is what enables curved drilling. It is made of a premium-grade steel which has a slight angle that can range from 0 to 3 degrees. Using this segment of the mud motor, the directional driller can orient the motor to drill in a specific direction, rather than drilling a straight line. To achieve the desired well geometry, operators have to carefully calculate the direction of drilling using highly reliable MWD tools.
The power section
This section contains the top sub, rotor catch, stator, and rotor. Here is where the hydraulic energy of the drilling fluid is converted into rotational horsepower.
At ProDirectional, our power sections are tuned for hard rock, soft shale, highly interbedded rock, and many other drilling environments. We also have elastomers for water or oil-based mud that can be used for standard or high-temperature drilling environments.
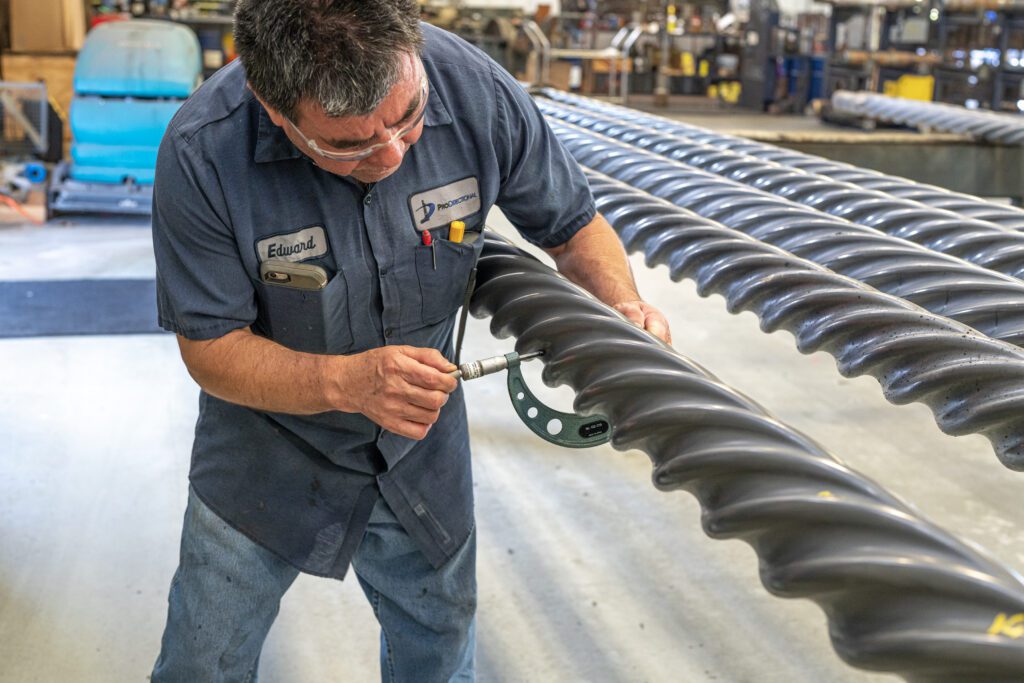
The difference application engineering makes
There are many service providers that offer operators mud motor drilling equipment. What makes our drilling motors different? It has something to do with the 100,000,000+ feet of drilling experience we have under our belts, combined with our focus on application engineering.
Unlike other service providers that simply purchase or rent mud motor technology from manufacturers and then use them in the field, we take a different approach.
In order to exceed the performance goals of our customers, we optimize the drilling technology based on our extensive field experience. Every time our team goes out into the field, we learn from the challenges the different geographies create and then use that information to further optimize the equipment.
This results in less downtime and minimizes non-productive time because our mud motors are highly reliable. They have been tried and tested, optimized, and then tried and tested again.
Not only that, but we also repair and maintain all of our own equipment instead of letting third parties provide that service. This enables us to be well-informed about the wear and tear on each mud motor component so that we can get ahead of any issues before they arise. Quality control is something we take very seriously.
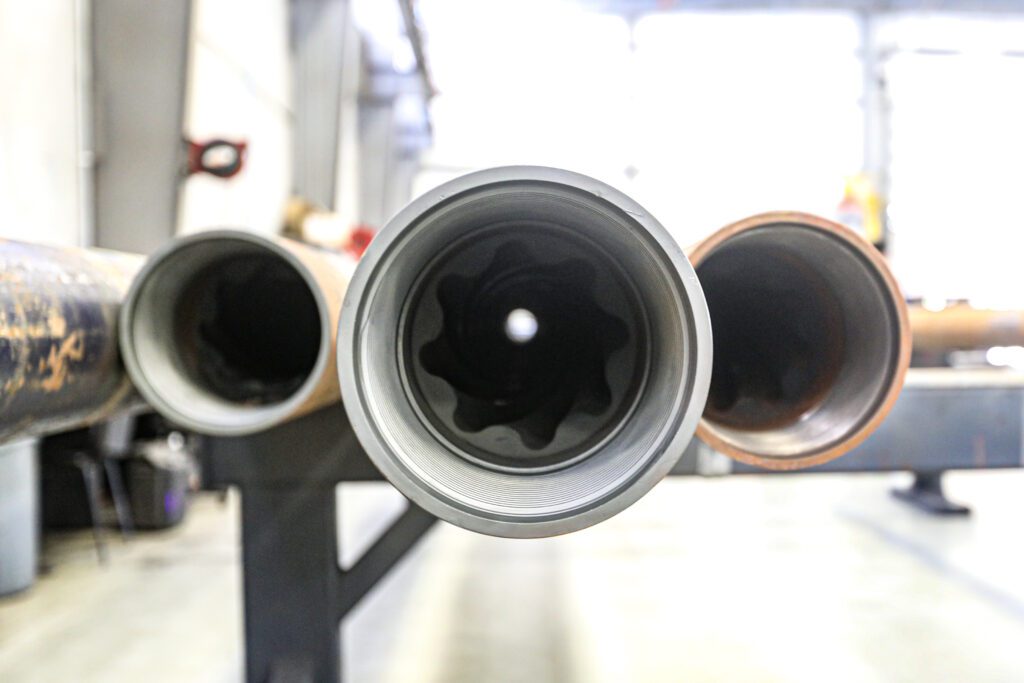
ProDirectional’s application engineering highlights
Here’s how we ensure our mud motor technology never fails in the field:
- Optimization and refinement: We have engineered the proprietary driveline and lower end based on our field experience to minimize non-productive time.
- Extreme power: We have sourced the most reliable power sections in the industry to ensure maximum power is delivered to the drill bit.
- Quality control: We reinforce our stringent quality standards with a full department that is dedicated to the repair and maintenance of our equipment.
- Innovative processes: Instead of a manual approach, we digitally track each mud motor component to ensure all repair and maintenance is up to date.
- Professional expertise: Our application engineering team consults with customers to determine the best mud motor configuration for their geography and performance goals.
Continuous improvement: The job is never done at ProDirectional. Our engineers are always updating our design and equipment to better perform in the field.
Reliable mud motor drilling for your application
Don’t settle for any mud motor. If you want to avoid non-productive time on your well and eliminate extra trips downhole, get in touch with ProDirectional today to learn more about our mud motor technology, how it works, and what configurations our application engineers recommend for your well.
Recent Articles
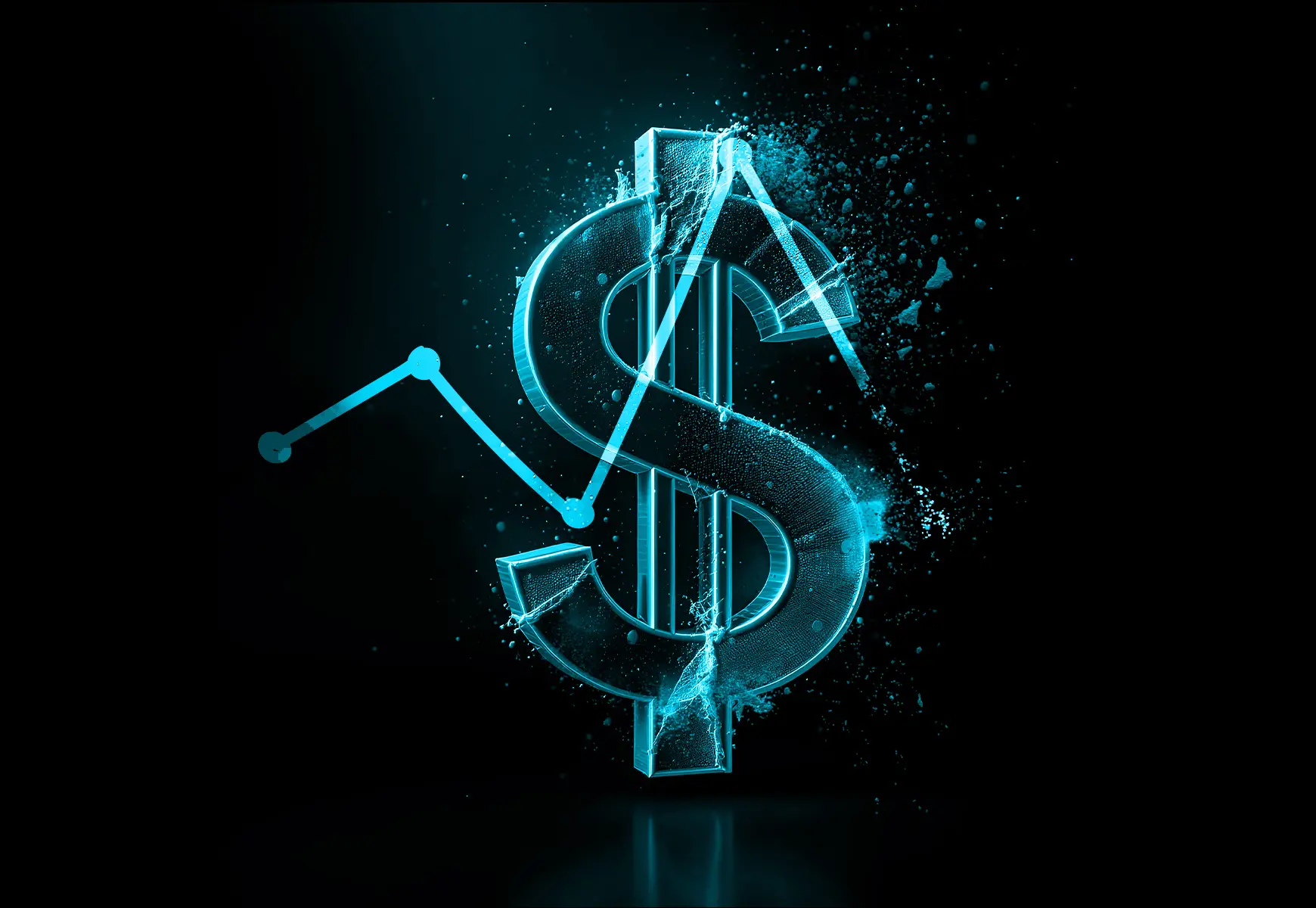
Why Best Value Beats Lowest Price in Directional Drilling
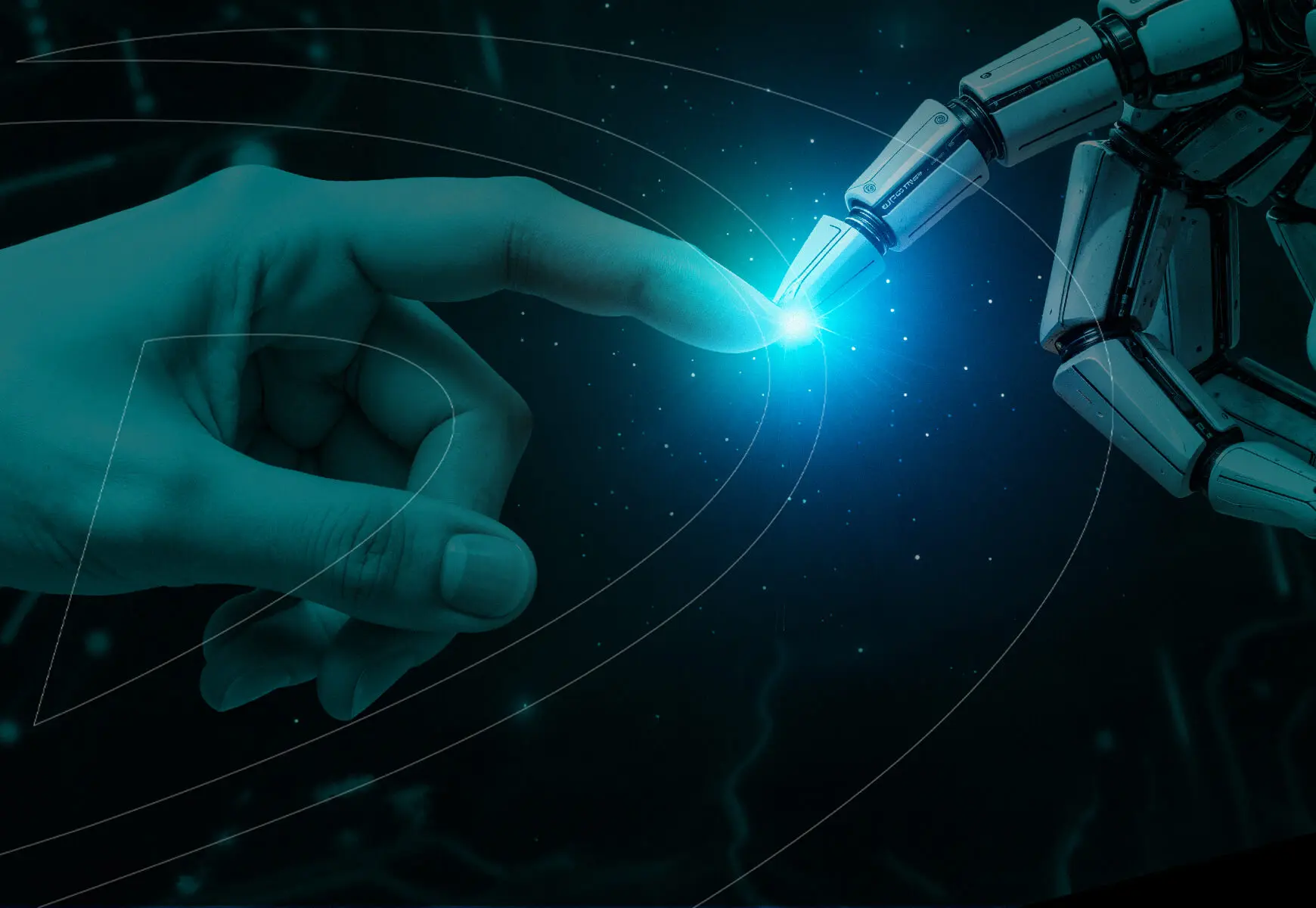
Automation in Directional Drilling: Why People Still Matter and How GUIDE ROC Delivers Both
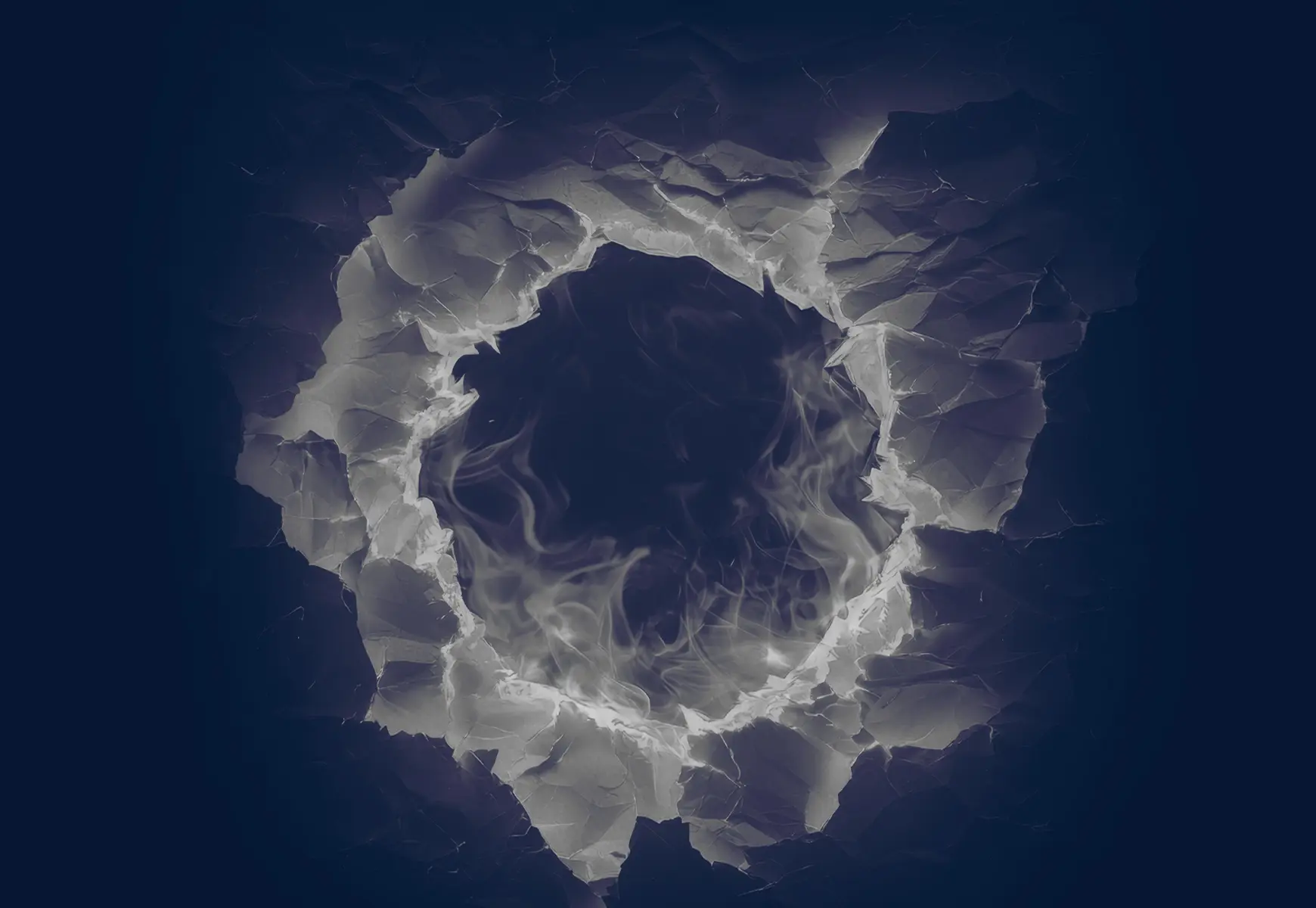
Turning Up The Heat: Providing Reliability in Hot Hole Environments
Built, Not Bought: The ProDirectional Advantage in MWD Services and Technology
A leap forward in rotary steerable system connectivity
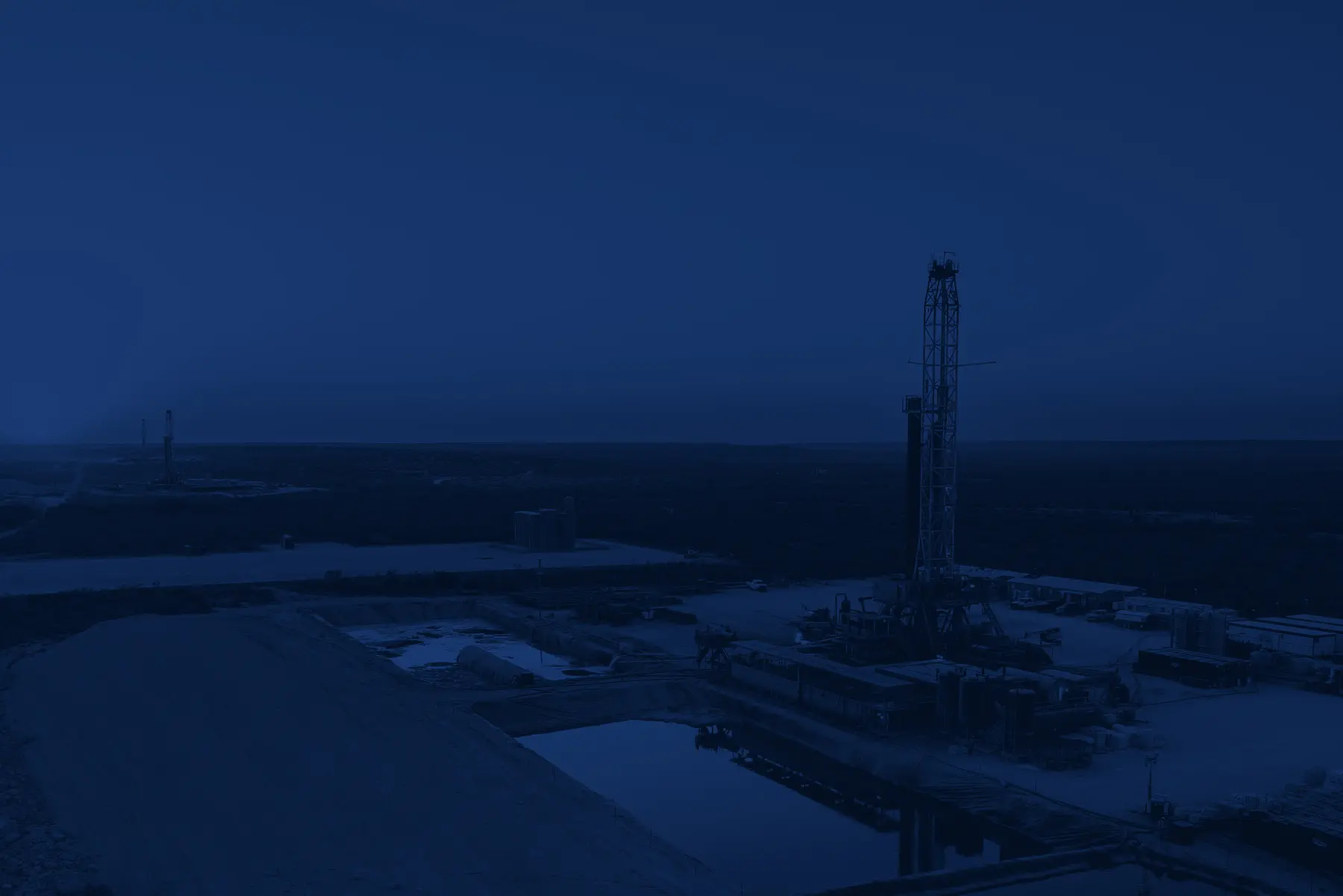
What client success looks like at ProDirectional
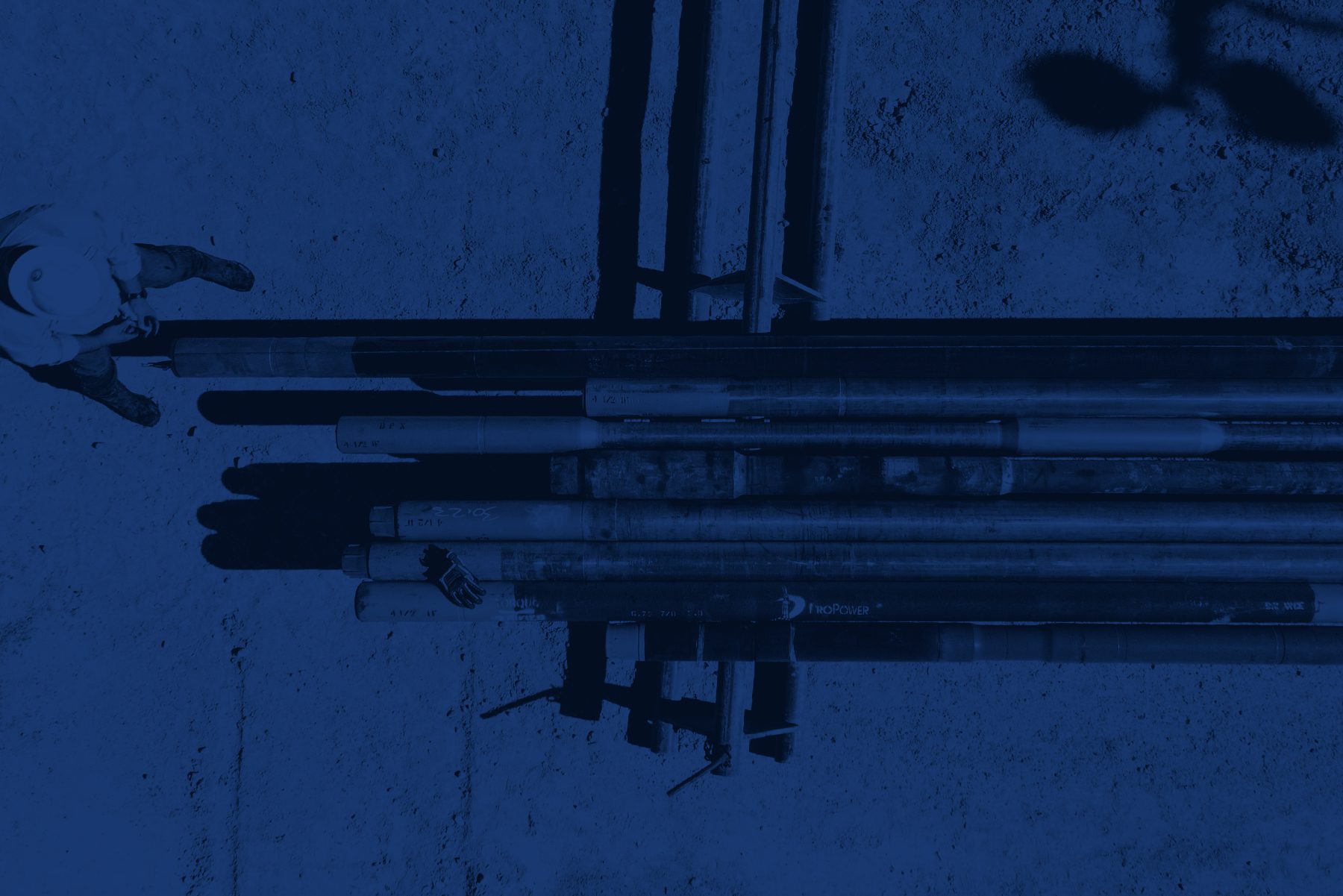
How does a mud motor work?
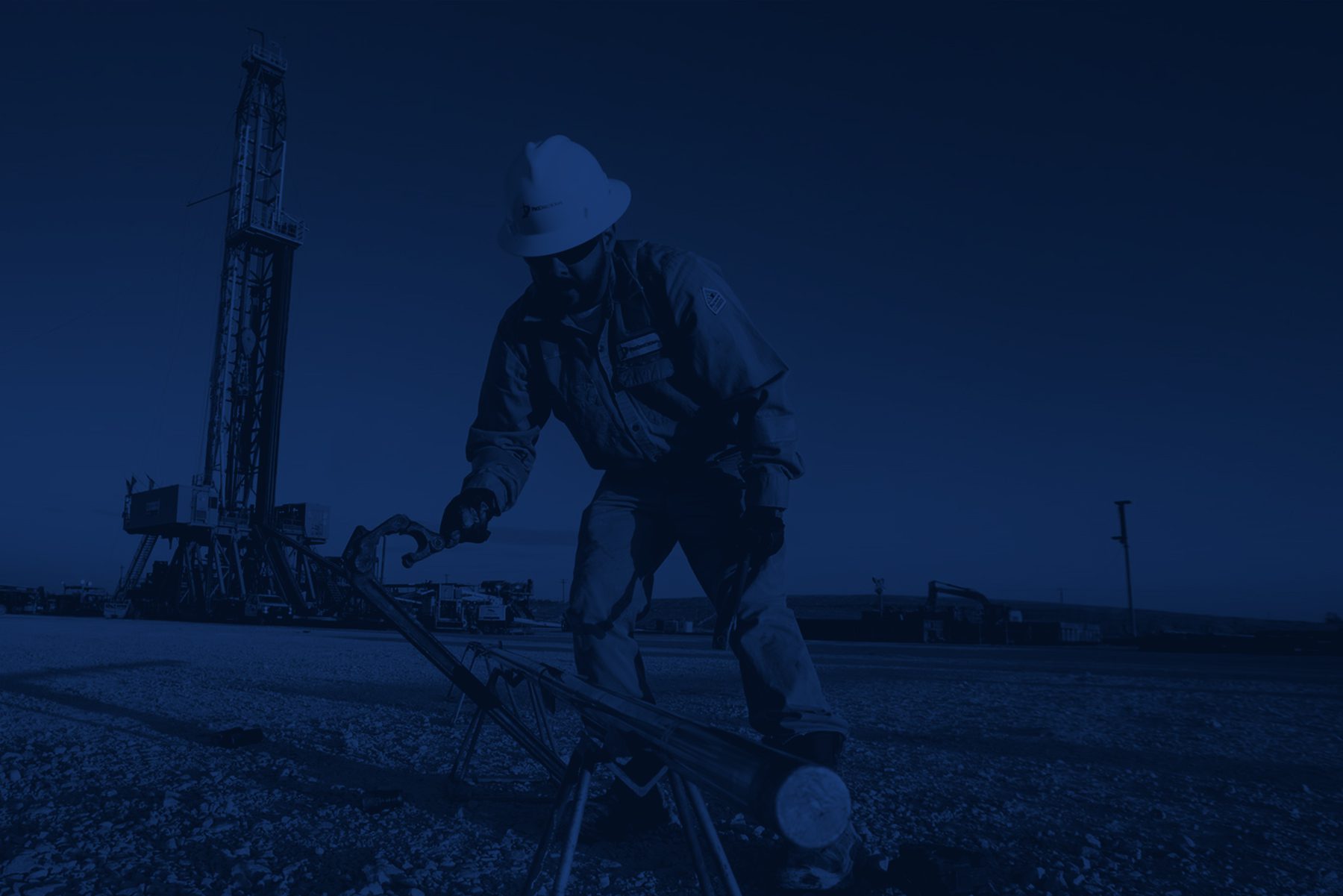
Application specific MWD tools and directional drilling technology will save you time and money
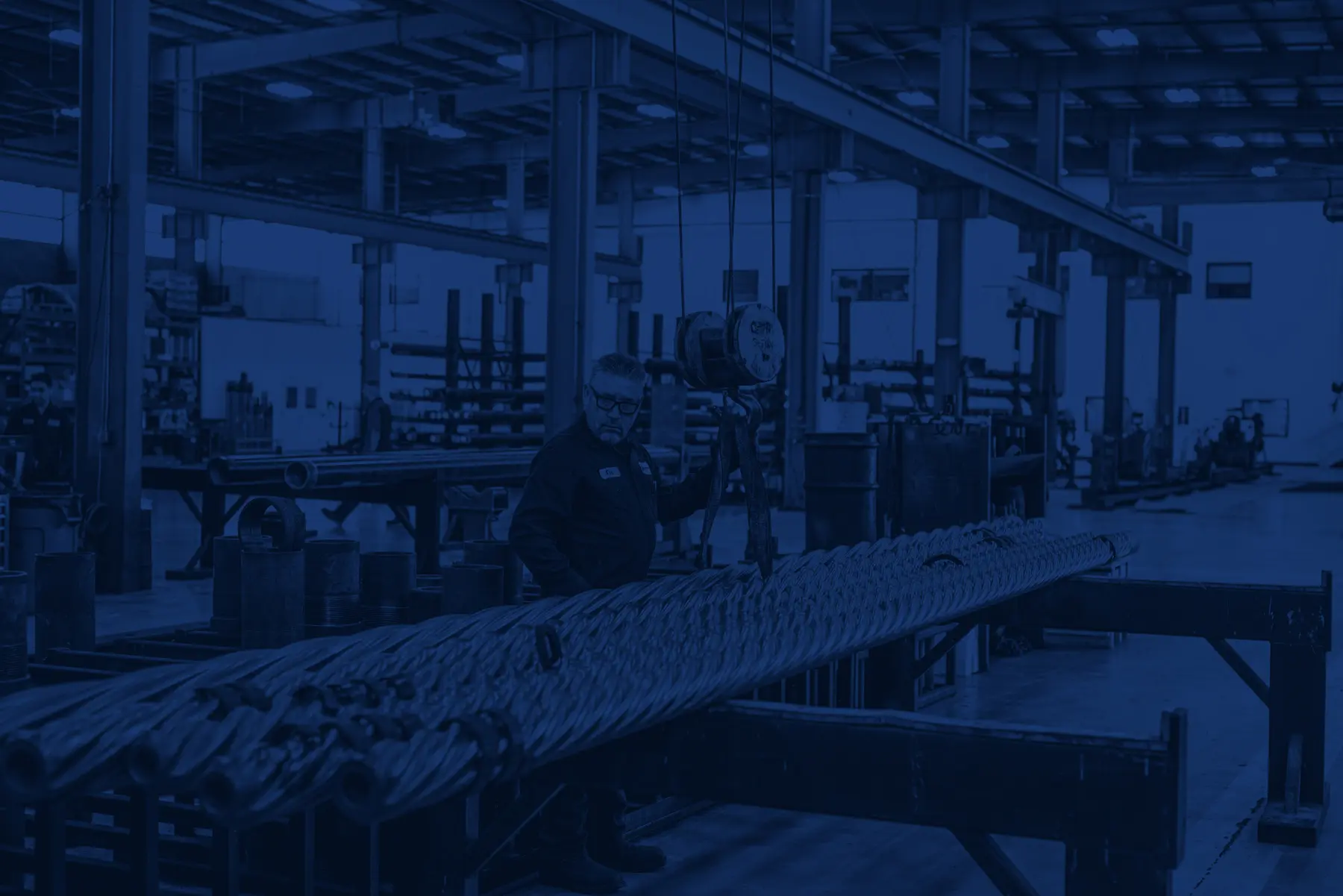
You can’t afford not to use highly engineered mud motor technology
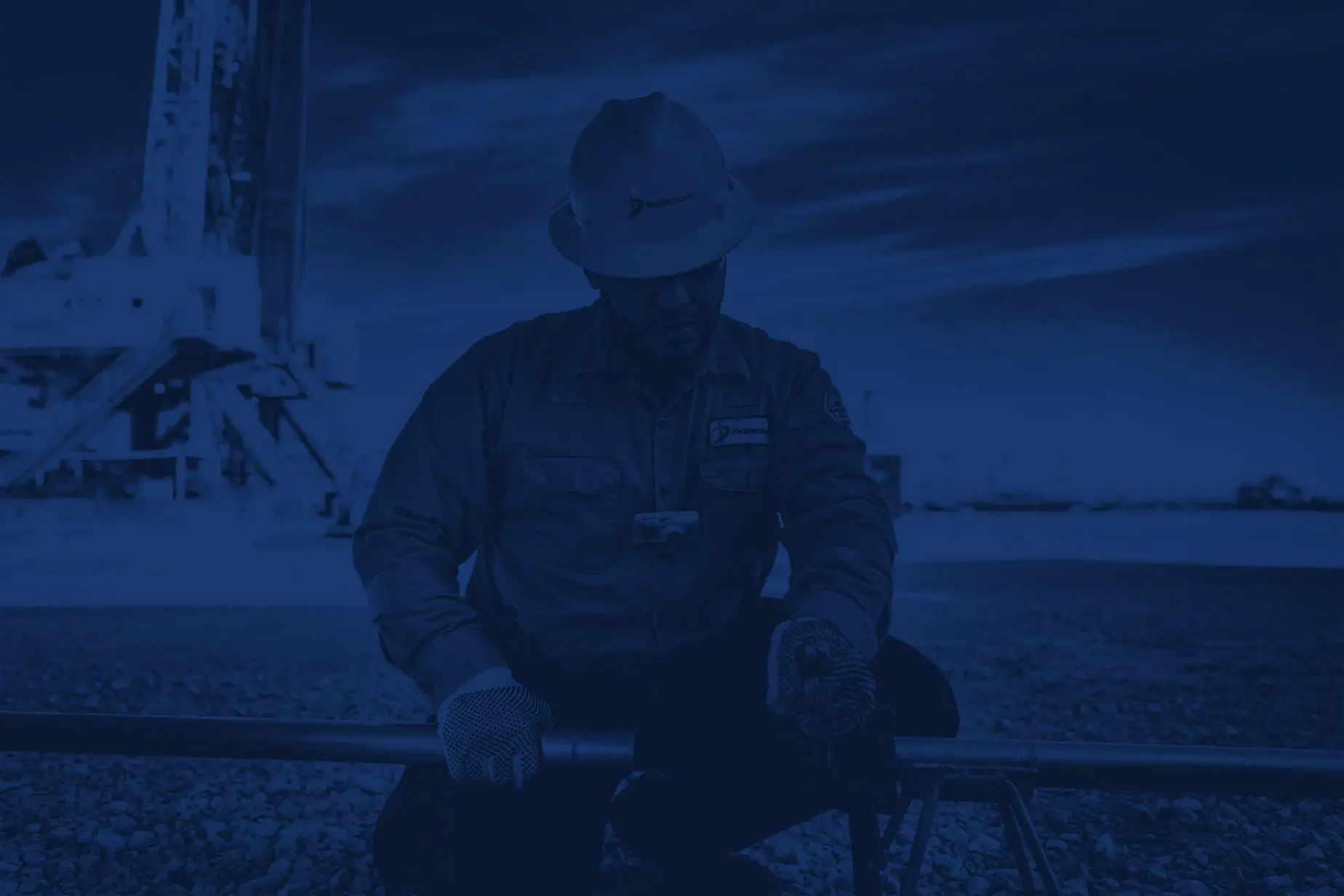