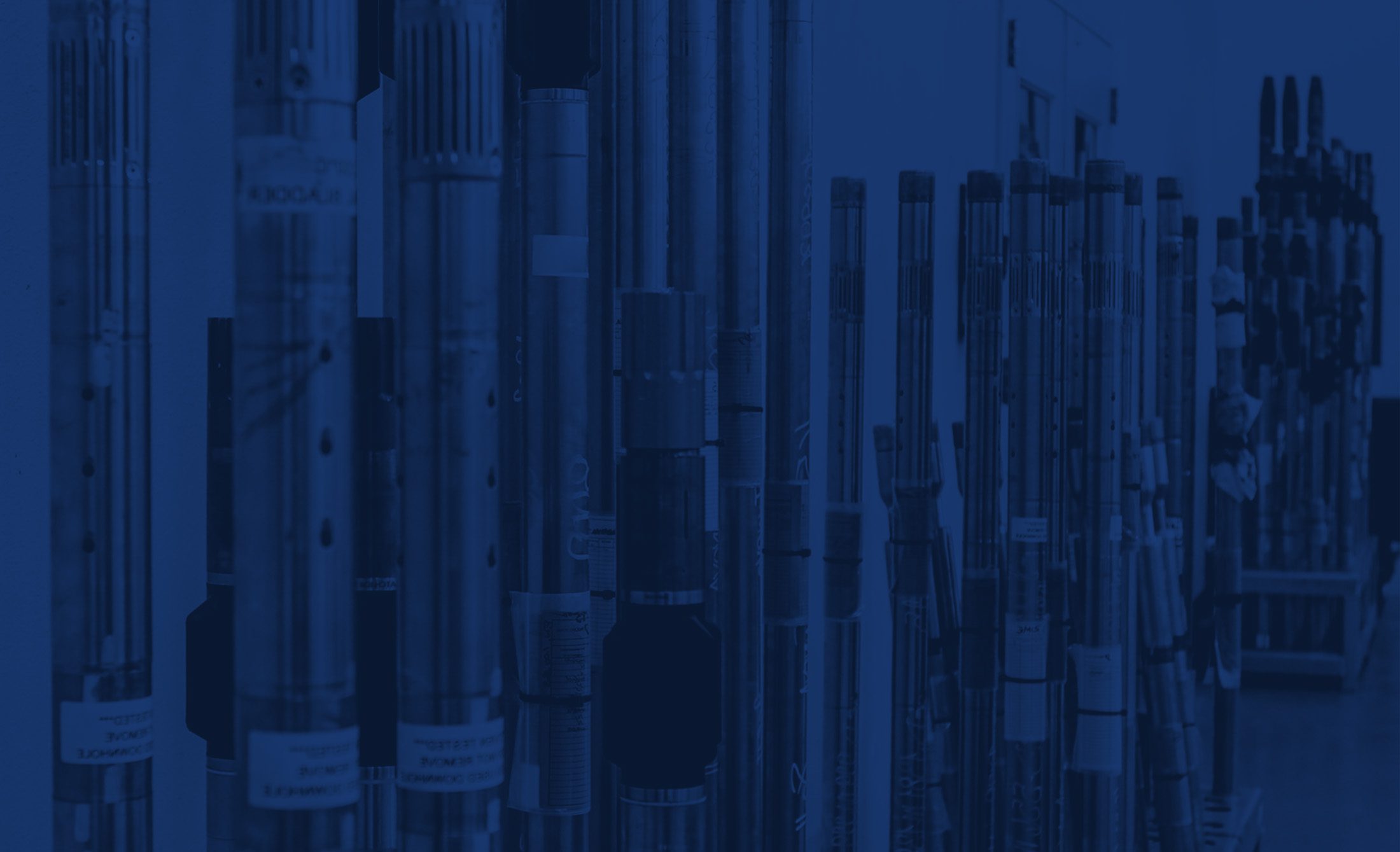
Pro ShockStop
Enhanced MWD reliability through minimized tool shock and vibration.
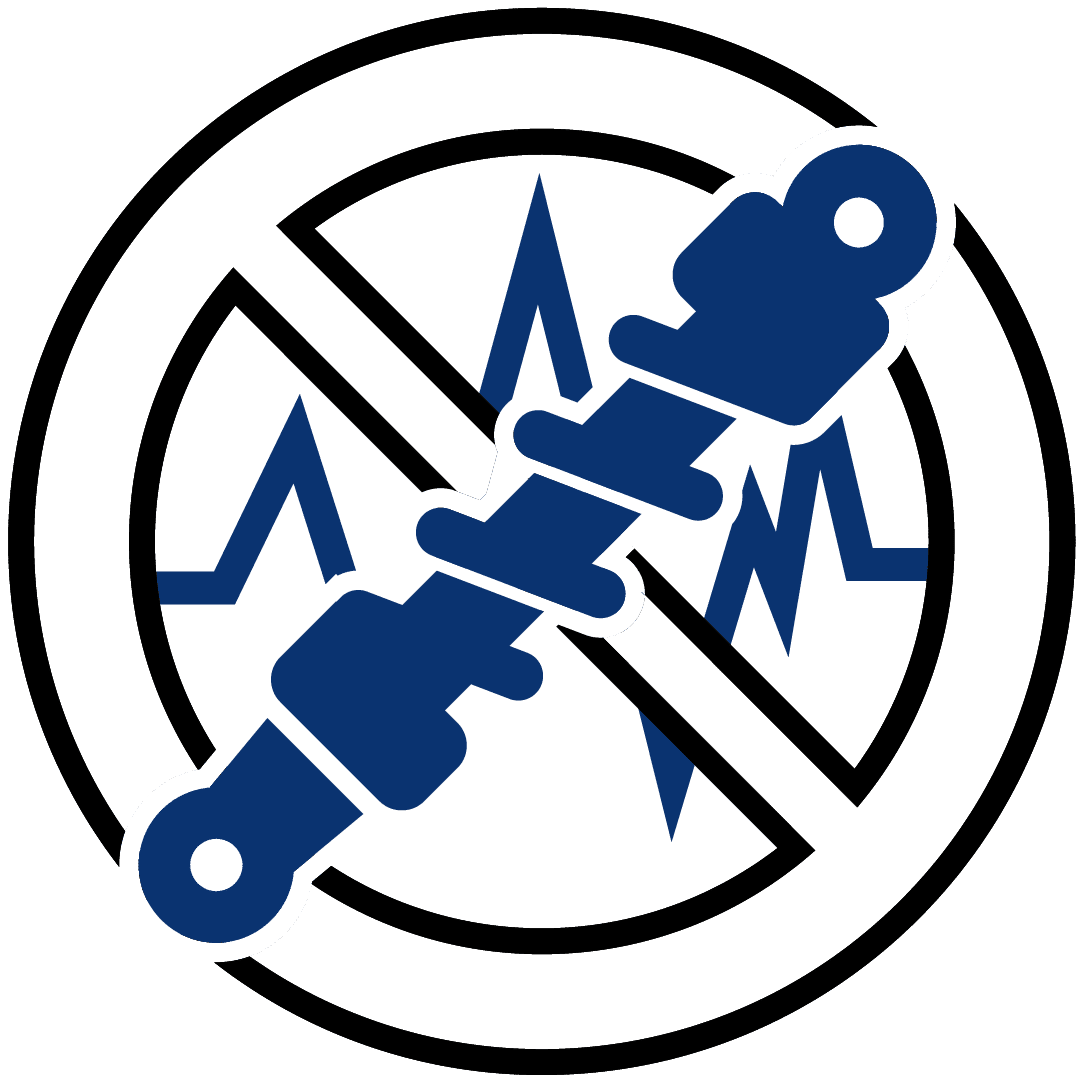
Drilling is violent. Our vibration dampening technology keeps components from being damaged.
Downhole shock and vibration are significant environmental factors that influence component reliability in MWD systems. Shock and vibe is unavoidable in all drilling, and in many cases, it’s not efficient to minimize it while drilling performance is exceeding expectations. Although vibration can be reduced by optimizing operating parameters, it can never be fully eliminated.
However, as a result of the axial shock and vibration, drilling components are at risk of being damaged, resulting in extra trips due to equipment failure. To mitigate this risk of NPT, ProDirectional developed the Pro ShockStop technology to isolate the MWD ecosystem from these damaging conditions.
A proprietary design approach that sets us apart
The market is full of shock and vibration mitigation technologies — many of which quickly disappoint clients. What makes Pro ShockStop different? Our technology was developed by our highly experienced engineers, who look at drilling from a holistic approach — not just from an MWD perspective. ProDirectional is a company that has drilled tens of thousands of wells, giving us insight into downhole drilling and vibration signatures that MWD component manufacturers simply don’t have.
Developed in-house, our technology is optimized to seamlessly integrate with our Sprint, Octane, and OctaneXT MWD tool strings. We continually refine and upgrade our Pro ShockStop technology to better serve our clients and further reduce the potential for failure.
Pro ShockStop reduces NPT in even the most rigorous conditions
At ProDirectional, we use our Pro ShockStop technology on every well we drill, because this component has been designed and engineered to provide industry-leading reliability — no matter the environment.
We develop and source best-in-class mechanical and electrical systems for our MWD ecosystems. As part of the development process, we engineer in mounting solutions and features that reduce the impact of vibration on electrical components. As these tools are used, we repair and maintain the technology to standards that are substantially higher than what is commonly seen in the industry. And then when the tools are run in the field, we employ best operating practices and the Pro ShockStop to minimize axial shock and vibration levels experienced by the MWD system.
What our clients experience with ProDirectional is high reliability of all MWD components, fewer trips to repair damages, and minimized non-productive time.
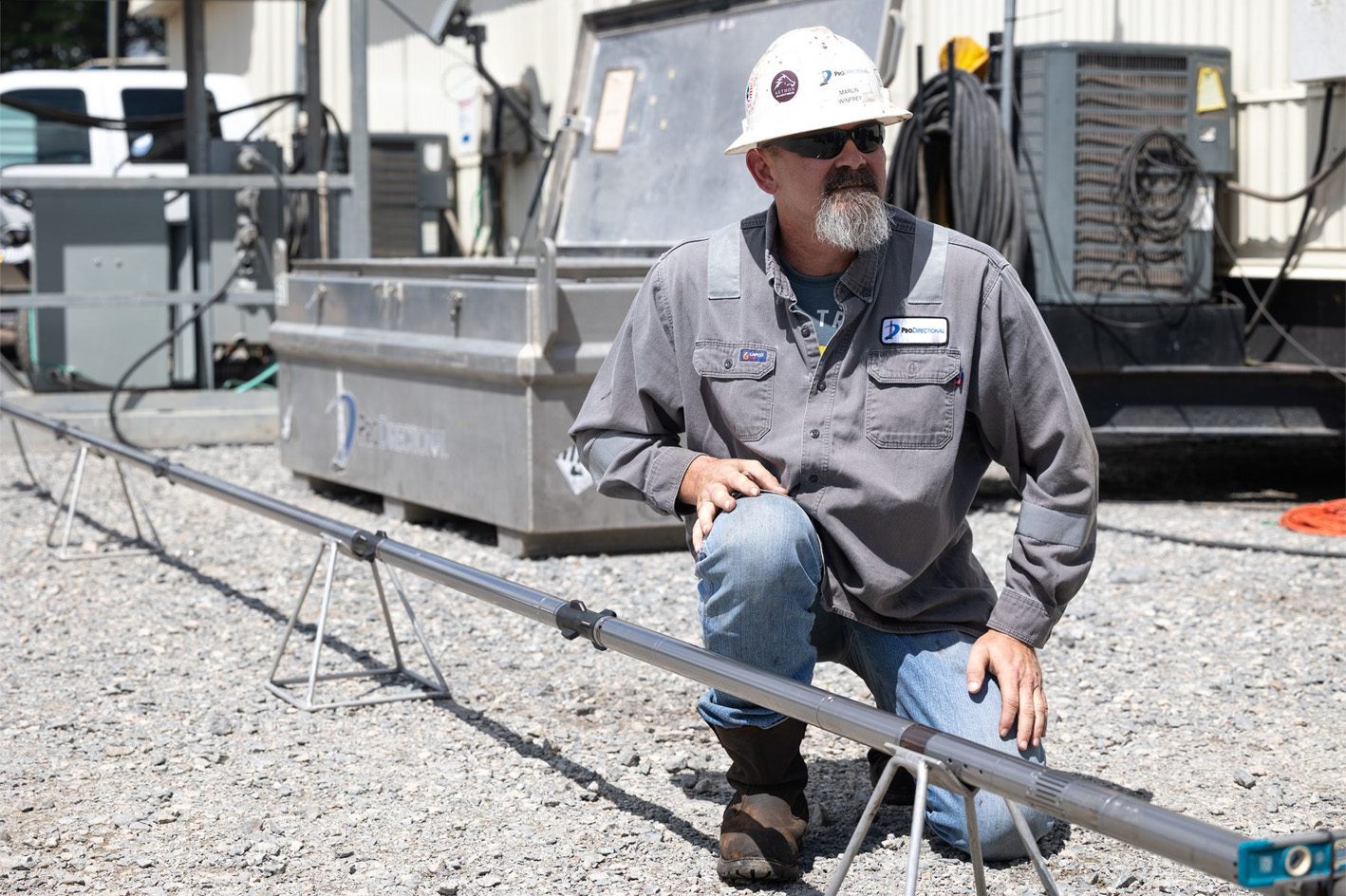
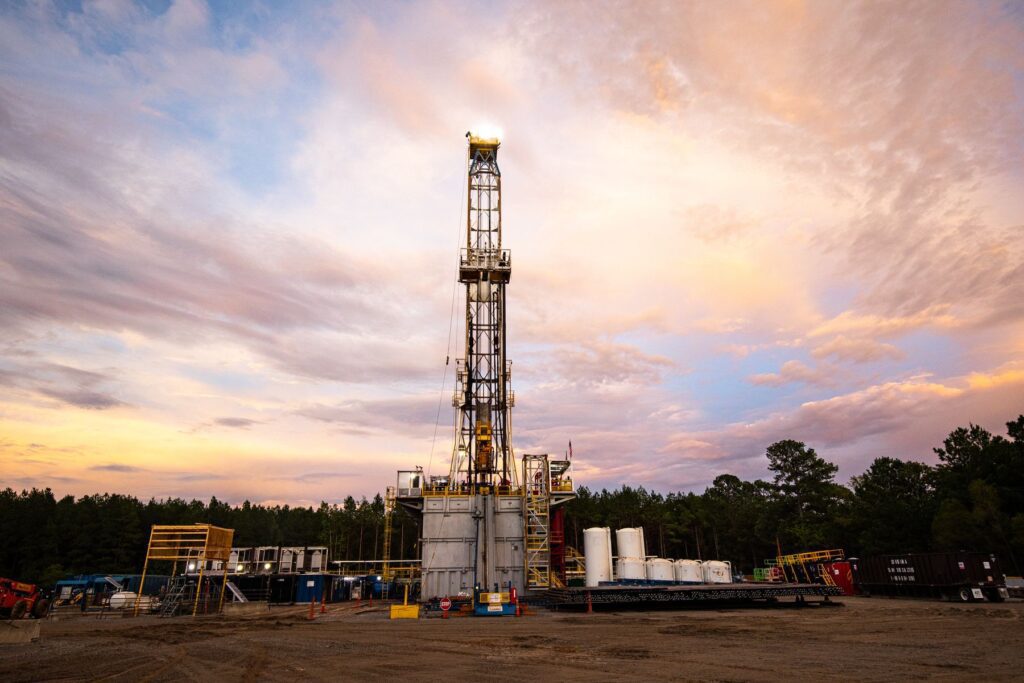
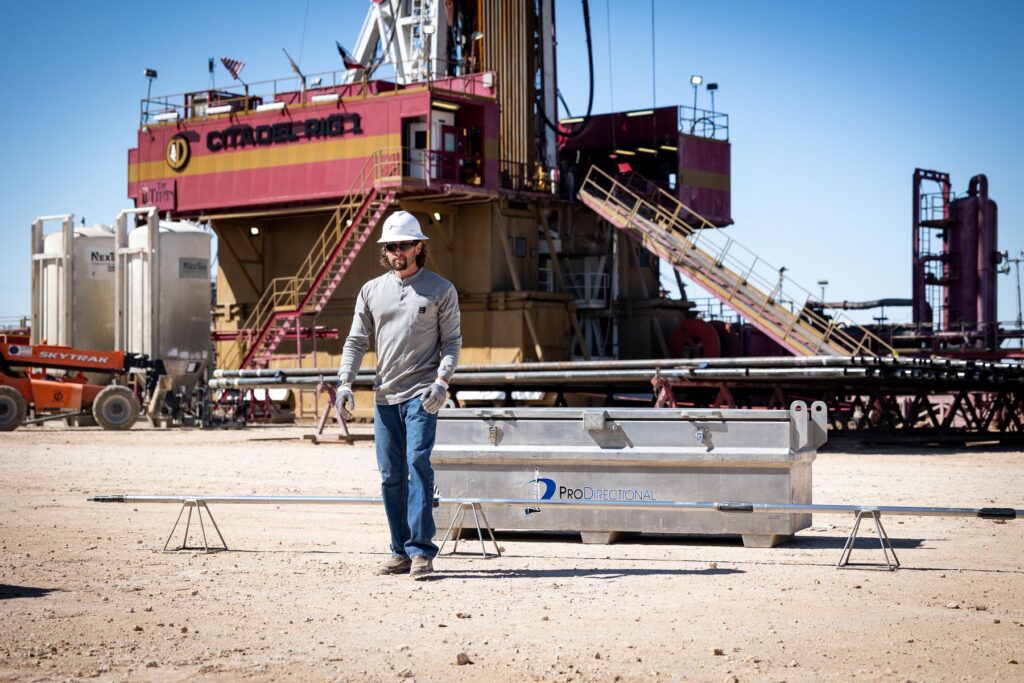